2024.12.13:New Blog Post: An Introduction to PLM – Product Lifecycle Management
This CIMdata blog posting simplifies what a PLM solution is, starting from the basics: the product structure / Bill Of Materials (BOM). It also addresses the strategic and organizational impacts of PLM solutions and provides some useful statistics on the main players in the market.
Highlights Include:
- What is a PLM solution?
- How do PLM solutions differ from ERPs?
- What are the impacts of a PLM solution?
- When is a PLM solution essential?
- Who are the main players in the market?
Read the full blog post in English here.
Read the full blog post in French here.
Monday, December 09, 2024
An Introduction to PLM – Product Lifecycle Management
Written by Laurent Finck
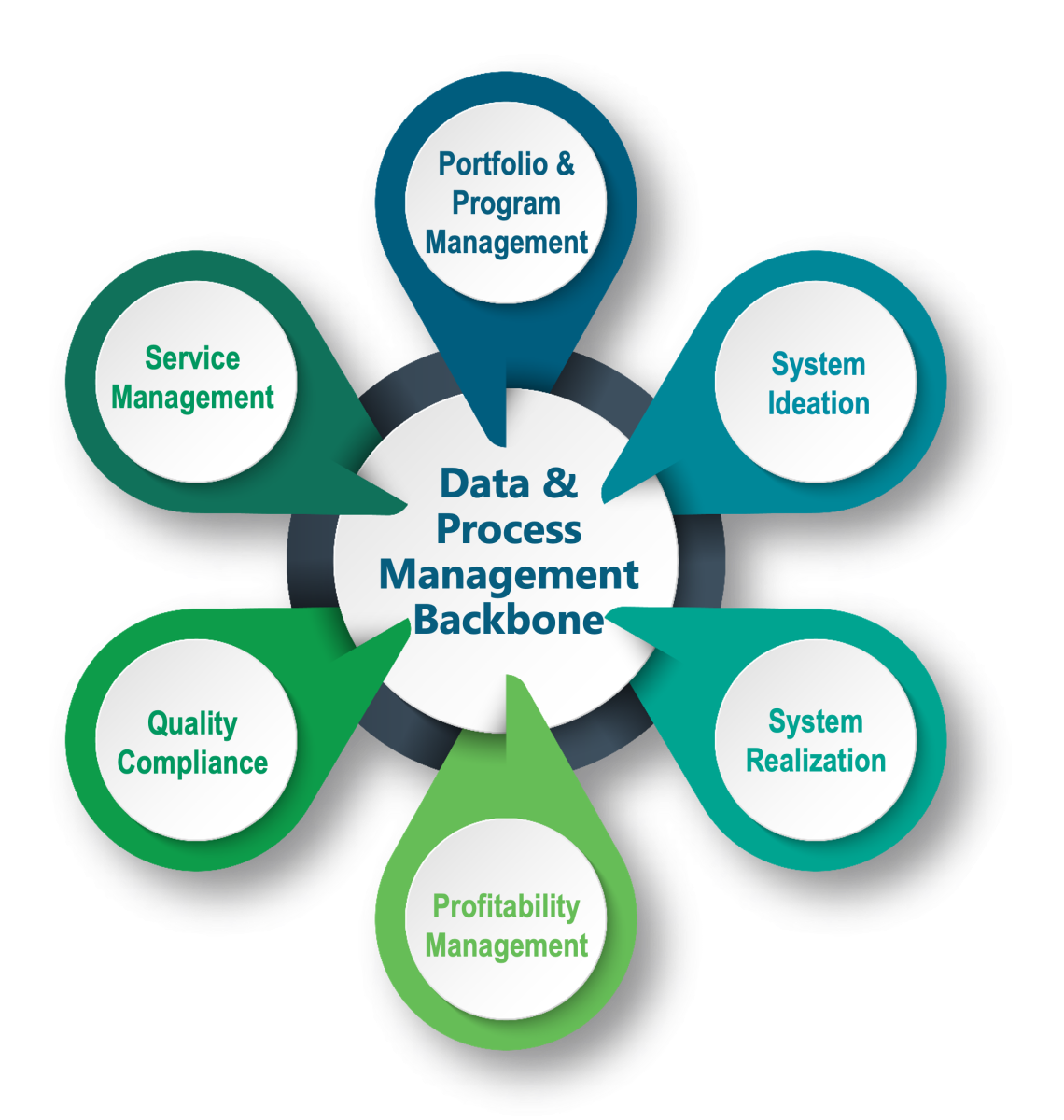
The industry of the future and the digitalization of industrial companies are bringing to the forefront information technology solutions that were not very well known 10 years ago: PLM solutions. What are they, what do they bring, why are they strategic, how do they coordinate with ERPs, and who are the main players?
What is a PLM Solution?
To develop, produce, and maintain a product, different functions, and organizations collaborate: R&D first, then the design office, then the methods office, purchasing, production, quality, marketing, maintenance, etc.
Until a few years ago, all these departments intervened successively and separately, and were the subject of information exchanges that all had to be synchronized to ensure that each department was working on the right version of the product within their part of the value chain (R&D; production and sales; maintenance and support). For example, it was necessary to ensure that when purchasing was looking for a component supplier, the design office had not already introduced a variant of the component in question, which would make the result of the purchasing work obsolete or even incompatible with the new version designed and soon to be launched in production.
Today, the data and processes generated during these different stages (CAD models and plans, documentation, definition of the manufacturing process, product nomenclature, service documents, catalogs, etc.) can be accessed through a virtual space that all associated partners can access: The R&D department, those responsible for designing the product, the manufacturers and partners who will manufacture it, the services that will install or maintain it, and the marketing that will promote and sell it. Access to a “single logical source of truth” is possible, in which the coordination of these accesses implements the concept of product lifecycle management (or PLM ): All stakeholders with a single and central description of the object in question for each of its variants, work more quickly, more efficiently, and more serenely because they coordinate better with each other. Thus, a PLM solution organizes and federates all the roles that must have access to the data and processes related to the product to fulfill their function.
Thus, a PLM solution manages a company’s product-related data and the knowledge attached to them throughout the product’s life. This fundamentally distinguishes it from ERP, which manages the resources needed to manufacture and sell the company’s products.
At the base of PLM solutions are some essential notions. One of the most important is product nomenclature.
Product Nomenclature : CAD-BOM, eBOM, mBOM, sBOM
Some definitions to begin with.
- CAD: Computer-Aided Design
- BOM: Bill Of Materials, or nomenclature
The CAD-BOM, or nomenclature of what was drawn by the design office. Commonly called “As-designed”
The CAD-BOM is the first of the nomenclatures from the design office. The design office designs the products and their components and draws the plans (today in 3D on CAD tools, and in the past in 2D with the famous plans that industrial design specialists produced). The CAD-BOM is the list of components of a product that have a plan.
eBOM – Engineering BOM
The list of components of a product that have a drawing is not necessarily sufficient to assemble them into a product: the CAD-BOM does not contain, for example, the greases or glues necessary for assembly. The eBOM contains, in addition to the components that have a drawing, those that are necessary for assembly. The eBOM provides all the components needed to manufacture the product.
The eBOM and CAD-BOM are provided by the Design Office.
mBOM: Manufacturing BOM; Manufacturing Bill of Materials
The mBOM organizes components to reflect the manufacturing process. Manufacturing sites, sourcing methods, and manufacturing processes are the customers of the mBOM. mBOMs are produced by the methods office, which uses the eBOM reference as a starting point and reorganizes it into mBOMs.
sBOM: Service BOM; Services Bill of Material
An sBOM defines all the components, parts, tools, and materials needed to perform maintenance, repairs, or service tasks on a product or piece of equipment. It also includes the service-specific information required to ensure proper functionality and compliance during these activities. Unlike a traditional BOM, which is primarily used for manufacturing, an sBOM is tailored for after-sales services and field operations.
PLM and ERP
ERP manages data and processes for managing company resources: Offers and quotes, customer orders, purchases, inventory management, production launches, transport, accounting, and finance.
PLM manages data and processes related to the company’s product development and modification process: Component data (dimensions and plans, materials and physical characteristics, strength, weight, etc.), technical documentation, manufacturing processes (machining, assembly), and development and modification processes.
The ERP, therefore, manages the resources needed to manufacture and sell products whose characteristics are managed by the PLM. The two systems exchange at least the mBOM, which is generally sent from the PLM to the ERP.

PLM solutions do not necessarily meet the needs of all business models: For a buy-sell activity, for example, only an ERP is necessary because the company’s activity does not require a BOM or technical design. Similarly, activities with simple BOMs and at an assembly level (for example, packaging of purchased products) can be very well managed in an ERP.
On the other hand, as soon as a technical design effort must be made, the question of using a PLM solution may arise. For example, a service provider that assembled its servers to operate its cloud service, managed at the start of its operations its bills of materials (one-level BOMs) in Microsoft Excel and SAP. Confronted with the growing diversity of its servers, it investigated the benefits of a PLM solution to simplify and streamline its design operations. Thus, the more complex the product designed and sold, the more essential it becomes to use a PLM solution to manage this complexity. Car manufacturers, for example, who must manage the design and assembly of 10,000 parts in vehicles with multiple variants, cannot do without a PLM solution.
Impact of PLM Solutions
The implementation of PLM solutions has profound organizational, operational, and strategic impacts on the company that deploys them:
- Organizational because by centralizing product information in a single location so that departments have access to a “single logical source of truth,” we profoundly change the company’s processes and systems.
- Operational because these systems allow the implementation of the concept of digital continuity (Digital Thread), that is to say, the connection of all departments to unique and valid data for each product variant. Not only can maintenance and support services know everything about the product in question, but R&D can also access production, quality, and even usage information when the product is connected. One of the drivers of the IoT revolution comes from there.
- Strategic because these systems provide the advantage of accelerating the process of developing and introducing new products to the market (NPI Process, New Product Introduction) while reducing the overall cost. The fluidity of the exchange of always up-to-date information between all stakeholders is the key element of this advantage, which becomes all the more competitive and strategic as the products are complex, with multiple variants, and with a high update frequency. Smartphones, for example, evolve in less than a year and are sold in several variants that depend on the countries in which they are sold. Adapting quickly to market changes is a strategic advantage.
In a market of increasingly complex products sold to customers who demand more and more new features and variants at a high frequency, a PLM solution is essential.
The choice of a PLM solution is therefore not neutral for the organization because to deliver all its promises, it will have sensitive organizational and operational consequences. This always requires clarifying the strategy and studying the needs prior to the investment to ensure the adequacy of the chosen solution to current and future needs.
PLM: Key Players
There are many players operating in the PLM market, but the market remains concentrated among a few leaders, as shown in the following graph:
Source: CIMdata 2024 PLM Market Solution Provider Report
There are many other providers that specialize their solutions by industry or technology. Let us mention BOM. com (now Arena Solutions, a PTC solution), one of the first to introduce a PLM solution in SaaS mode, Aras, Oracle PLM, SAP PLM, Odoo PLM, Aveva, Centric Software, Lascom, BeCPG, Slerant, Specpage, Infor PLM, CGS, Audros PLM, Lectra, and Arena.
Each player has its strengths and weaknesses, its licensing and maintenance costs, its contractualization method, its vision of the future, its ability to deliver on the promises made, its network of integrators capable of deploying its solutions, its probability of sustainability, and its shareholders. All these are essential elements in choosing a solution, the individual importance of which must be ensured regarding needs and issues.
Please let me know your thoughts on this topic by sharing them in the comments section of this blog!
Or contact me directly at l.finck@CIMdata.com
Laurent
Laurent Finck
Email l.finck@cimdata.com
Latest from Laurent Finck
- Introduction au PLM – Product Lifecycle Management
- Le PLM, clé de l’Industrie du Futur
- PLM, the Key to the Industry of the Future
MORE…
Le PLM, clé de l’Industrie du Futur »
« Introduction au PLM – Product Lifecycle Management