2024.12.11:Addressing the Cost of Sustainability During Early Product Development (Commentary)
Key Takeaways
- Effectively addressing sustainability factors throughout the product lifecycle is becoming a critical business imperative. Customers increasingly expect products—and the processes behind their development, delivery, and operation—to align with ever more stringent sustainability standards.
- Companies that embed sustainability evaluations early in their development process and across their supply chain will have a competitive advantage in the marketplace, improve their efficiency and resiliency, and meet sustainability goals, which leads to long-term profitability
- Manufacturers across all industries need to adopt an integrated approach to calculating both cost and carbon footprint earlier in their design and development processes.
- Teamcenter Product Cost Management provides the ability to make better decisions based on cost and carbon insights across the extended enterprise, which can lead to greater efficiencies, reduced product cost and carbon footprint, and greater resiliency.
- Siemens solutions for integrated Design, Manufacturing and Supply Chain are designed to enable companies to achieve better end-to-end sustainability and carbon footprint visibility across the extended product lifecycle and supply chain which facilitates better planning and optimizes execution by shrinking transport distances, eliminating deadheading and improving consolidation and bundling.
Introduction
Global warming and the resulting climate change and sustainability challenges represent the most significant threat to life on Earth. Its effects are not only felt by the current generation but will also profoundly impact future generations unless decisive actions are taken to transition to a more sustainable economy.[1]
More and more consumers, investors, companies, and policymakers are recognizing the realities of climate change, resource scarcity, and the need to transition to more sustainable practices that focus companies on waste elimination and decarbonization of their products. The number of companies reducing their carbon footprint by committing to net-zero emissions and other sustainability targets is dramatically increasing, including those of participants in their extended supply chains.
There are currently more than 5,500 companies with validated net-zero Science Based Target Initiative targets.[2] Also, there are over 500 signatories to the Climate pledge, which vow to meet the Paris Climate Agreement 10 years earlier.[3]
Current State of Addressing the Sustainability Challenge
Today, companies across many industry sectors are increasingly impacted by the need to reduce carbon emissions, an effort complicated by the interconnected nature of the global economy. Many industries depend on processes that produce greenhouse gases (GHGs), especially carbon dioxide (CO₂e), making improving sustainability a universal concern.
Industries rely heavily on energy, much of which still comes from fossil fuels like coal, oil, and natural gas. These sources are major contributors to carbon emissions that cause global warming. To meet sustainability goals, companies must transition toward renewable, clean energy sources, enhance energy efficiency, and reduce waste wherever possible throughout the product lifecycle.
A product’s carbon footprint—or its “embodied carbon”—refers to the total GHG emissions released throughout its lifecycle, from resource extraction and manufacturing to transportation, installation, usage, recycling, and disposal.
Most products and services are built on supply chains that cross multiple sectors and regions. Each step in the supply chain—from raw material extraction to final delivery— involves carbon emissions. To achieve meaningful sustainability, companies must tackle emissions not only within their own operations but also across these extended supply chains.
GHG emissions are broken down into three categories. Scope 1 includes direct emissions from owned resources such as fuel combustion onsite and by company-owned vehicles. Scope 2 covers indirect emissions from the generation of purchased energy. Scope 3 encompasses indirect emissions across a company’s upstream and downstream supply chain, including emissions related to business travel, purchased goods, waste generation, and other sources.
In the traditional “take, make, waste” linear economy, companies have traditionally prioritized time, cost and quality. But now, companies must also consider sustainability and regulatory compliance as they transition to a more circular economy where companies must strive to meet their sustainability targets and comply with regulatory requirements.
Governments and international organizations are increasingly enacting policies and regulations, such as carbon taxes, emission trading systems, and directives like the EU’s Corporate Sustainability Reporting Directive (CSRD), which mandates carbon reduction efforts across sectors. These policies drive manufacturers to lower their carbon footprint and adopt more circular and sustainable practices.
The challenge many companies face is their processes do not provide the needed end-to-end visibility of cost and sustainability data or control that information across the extended enterprise. The many disconnects in the value chain from conceptual design, cost and value engineering, procurement, logistics, manufacturing, and service processes as well as the interaction of upper management, suppliers, partners, and vendors creates a lack of transparency and acts as a barrier to making the right decisions on design, cost, and sustainability.
Solving the Sustainability Challenge
An integrated approach to calculating both cost and carbon footprint is essential for achieving sustainable practices. Such an approach can enable companies to reduce their Product Carbon Footprint (PCF), design sustainability into their products, eliminate waste, and identify key factors that affect costs, risks, and carbon emissions.
These insights enable stakeholders to “shift left”—making optimal decisions about cost and sustainability earlier in the product lifecycle. This enables cost and value engineers to better support sustainable design and cost optimization by having visibility into the carbon dioxide equivalent (CO₂e)—across materials, parts, and processes. They can simulate and iterate on material specifications to reduce carbon, weight, and hazardous materials, while better-managing product complexity and increasing sustainability through modularity, longevity, disassembly, reuse, and recycling. The procurement team can analyze the full impact of sourcing parts from suppliers in developing versus developed economies. Supply chain managers can also weigh the trade-offs among transportation costs, CO₂ emissions, risks, and lead times, which allows them to make informed decisions about efficient, sustainable, and cost-optimal transportation flows.
This integrated approach will also enable improved planning, control, monitoring, and optimization of the flow of goods, reducing inventory levels and mitigating risks. Improved transparency across a complex transportation network enables logistics systems to consider alternative transportation modes, balancing costs and reducing the CO₂e of the PCF. To gain even greater transparency and efficiency, sustainability efforts should extend beyond immediate upstream and downstream partners in the supply chain. A broader perspective enables management to make more informed strategic sourcing and operational decisions by providing greater visibility across the extended enterprise.
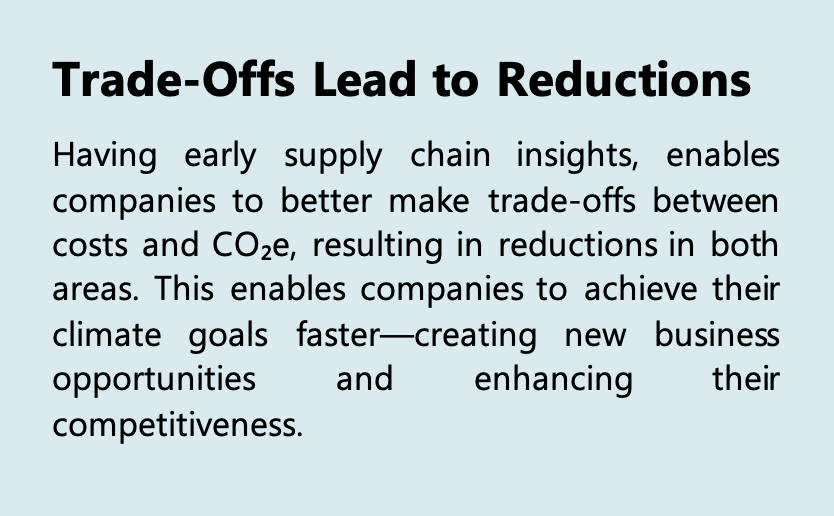
Decarbonization demands a change in product design, material selection, specifications, and supply chain practices. This provides a dual opportunity to capture the benefits of both lower CO₂e and potential cost savings enabling companies to dramatically improve their efficiency and resiliency. A resilient supply chain begins with product design transparency across the extended enterprise and the ability to iterate and improve both costs and sustainability. These insights enable creating better coordination and synchronized flow with production.
Using an integrated solution to transparently share CO₂e data and costs among designers, engineers, cost and value engineers, program managers, procurement, finance, sales, and upper management—as well as vendors, suppliers, and partners—reduces barriers, increases productivity, and minimizes risk. Linking a product cost management solution with PLM, ERP, TMS, supply chain execution, supply chain optimization, and design-to-source intelligence solutions provides a unified view of design, manufacturing, and supply chain activities. This fosters a convergence of efforts to achieve full control over risks, costs, and PCF.
Teamcenter Product Cost Management
Teamcenter® Product Cost Management, part of the Siemens Xcelerator business platform of software, hardware and services, is a comprehensive solution for managing product and tool cost, carbon footprint, and profitability calculations. It enables cost and value engineers, designers, procurement, and manufacturing teams to evaluate trade-offs between costs and CO₂e to make optimal decisions that balance PCF with the ideal product cost.

(Courtesy of Siemens)
Siemens Xcelerator portfolio is available both on-premises and as a SaaS cloud offering. Teamcenter Product Cost Management is based on a bottom-up approach for cost calculations. As shown in Figure 1, it uses a detailed product structure and defines the resulting material and process costs. The calculations are based on cost information for raw materials, purchased parts, work plans, and overhead. This results in detailed cost information that can be used for cost breakdowns and many other reports.
Carbon Footprint Calculator
The Teamcenter Carbon Footprint Calculator is part of the Teamcenter Product Cost Management solution, which follows the same bottom-up analysis workflow for CO₂e emissions, summing all emissions factors across the value chain. It includes data on direct emissions such as raw materials, semi-finished parts, machinery, energy, and tools, as well as upstream emissions from purchased parts, energy usage, transportation, and waste. Emissions tied to indirect costs, like overhead and logistics, and those from downstream activities like recycling and disposal are also included. Users can classify the detailed emissions data into the GHG Protocol scopes 1, 2, and 3, providing a view of emissions data, which supports eco-design strategies and resource-efficient design.
The Siemens solution approach capitalizes on the transparency and optimization that bottom-up target costing provides. The solution considers all the processes from extracting raw or recycled materials and manufacturing of precursors through the production of the final product to when it leaves the company’s gate (cradle-to-gate). Because the analysis is done at a granular level companies establish eco-design strategies such as design for resources.
Teamcenter Carbon Footprint Calculator includes benchmark data for labor, materials, machinery, energy, and manufacturing processes across global locations and suppliers. Information on cost and carbon footprint factors such as worldwide locations and suppliers is required to continuously increase the value proposition of purchased or self-manufactured components. Teamcenter Product Cost Management includes a database maintained up-to-date with benchmark data, such as labor costs, materials, machines, energy, and manufacturing processes, as well as an integrated cycle time calculator. This data makes reliable make-or-buy, relocation, and global sourcing analysis possible, which can be used to reduce manufacturing costs and carbon footprint.
Tool Costing, Profitability, and Simulation
The integrated tool-costing feature within Teamcenter Product Cost Management highlights the interactions between components and tool costs at different production volumes, bringing transparency and reliability to tool design. With the integrated profitability analysis, managers can forecast unit costs and prices over a product’s lifecycle, strengthening investment decisions.
Teamcenter Product Cost Management supports precise, rapid calculations on variants of complex assemblies and offers technical and economic “what-if” scenario simulations. By evaluating cost impacts from changes in commodity prices, labor costs, design adjustments, and transportation modes, users gain an early and transparent view of target costs, allowing for proactive cost management early in the product development process. This functionality also facilitates collaboration on complex calculations across divisions and sites.
Integration with Siemens and 3rd-Party Systems for Comprehensive Digital Twins
Teamcenter Product Cost Management is highly customizable, supporting integrations with Siemens solutions and third-party systems. It consolidates data such as Bill of Materials (BOMs), Bill of Processes (BOPs), and CAD files from PLM systems like Teamcenter; plant data and material prices from ERP systems; logistics costs and CO₂ emissions from logistics platforms such as Siemens Digital Logistics; and prices and risk factors for electronic parts from the Siemens Supplyframe Design-to-Source Intelligence (DSI) platform. This information can be consolidated and used in Teamcenter Product Cost Management during early stages of development, which enhances decision-making and makes possible the realization of the digital twin, including the cost and PCF.
Mr. Mark Reisig, CIMdata, Executive Consultant and Sustainability Practice Director, states “Companies using PLM to transparently share CO₂e and cost data across their extended enterprise not only reduce product carbon footprints but also foster greater collaboration, boost productivity, and lower risks, building a more resilient business.”
Applying an Integrated Strategy for Sustainability and Efficiency
To achieve ambitious company-wide sustainability goals, an integrated sustainability and efficiency strategy is essential. For manufacturers, this means that balancing operational performance, cost, and service requires seamless integration across product design and development, logistics (both internal and external), procurement, production, and material flow. By adopting the shift-left principle, companies can bring design, development, production, and logistics into closer alignment with sustainability goals earlier in the lifecycle process. CIMdata is impressed with Siemens’ comprehensive approach, which can enable companies to tackle today’s product lifecycle challenges holistically, balancing cost, risk, sustainability, and quality objectives effectively earlier in the process.
With its synchronized design, manufacturing, and logistics offering Siemens enables design teams to take a holistic view of environmental and economic factors, greatly enhancing the ability to create sustainable designs. By bringing sustainability considerations into the early stages of design and development, Siemens claims that companies can address up to 80% of a product’s environmental impact during product development while also optimizing costs.
Siemens’ solutions enable getting valuable insights to improve production planning through real-time supply chain data. Companies can simulate production processes, warehouse allocations, and supply chain flows using Siemens’ Plant Simulation (PlantSim) and Supply Chain Suite (SCS), which enables them to identify and eliminate logistical bottlenecks. These optimized simulations can increase production capacity while helping companies reduce CO₂e and logistics costs while avoiding unnecessary retooling and downtime.
In manufacturing, Siemens solutions for material tracking in production logistics enable precise planning and control of supply processes. Real-time transportation information from Siemens AX4 logistics platform enhances production scheduling and allows rapid adjustments to production orders when deviations occur, reducing CO₂ emissions and logistics costs, minimizing downtime, and avoiding retooling.
Siemens Supply Chain Solutions offer a comprehensive approach to planning and optimizing logistics networks, managing transportation flows across collaborative networks, and streamlining intralogistics. Through Supplyframe’s design-to-source (DSI) intelligence platform, companies can make informed sourcing decisions and balance cost, risk, and sustainability. Incorporating these supply chain insights early in product development reduces risk and promotes sustainability throughout the product lifecycle.
Shifting cost and CO₂e considerations to the early phases of design and development helps companies reduce costs and risks while meeting increasing strict regulatory requirements and responding to consumer demand for sustainable products.
Conclusion
CIMdata believes that companies that can embed sustainability insights early in the development process and across their supply chain have a competitive advantage in the marketplace—enabling them to improve their efficiency, resiliency, and sustainability, which leads to long-term profitability. Most of the environmental impact is determined in the early design and development stage of product development. When a company can shift cost and CO₂e to the left, they are far more able to reduce their PCF and make better decisions related to cost and sustainability.
CIMdata is impressed with Siemens Teamcenter Product Cost Management solution, which enables companies to make better decisions based on cost and carbon insights across the extended enterprise. This can lead to greater efficiencies, reduced product cost and carbon footprint, and achieve greater resiliency. The use of Siemens solutions for integrated Design, Manufacturing, and Supply Chain is an enabler to better end-to-end supply chain visibility, which facilitates improved planning and optimizes execution by shrinking distances, eliminating deadheading, and improving consolidation and bundling.
The Siemens Teamcenter Product Cost Management and Supply Chain Management solutions enable manufacturers to “shift-left” when addressing sustainability during design and along the entire product lifecycle. This enables teams to converge by transparently sharing CO₂e and cost, enabling better and greater collaboration and better decision making, that result in reducing their PCF and costs, but also boost productivity, and lower risks, building a more resilient extended enterprise.
CIMdata recommends that companies wishing to address their sustainability goals, reduce their PCF, lower their costs, and streamline their supply chain and logistics operations include Siemens Teamcenter Product Cost Management and Supply Chain Management solutions in their evaluation and selection process.
[1] Research for this paper was partially supported by Siemens Digital Industries Software.
[2] https://sciencebasedtargets.org/news/sbti-marks-5500-companies-with-validated-targets-announces-next-steps-in-transformation
[3]https://www.theclimatepledge.com/content/amazonclimatepledge/us/en/Stories/the-climate-pledge-now-has-over-500-signatories.html#:~:text=The%20Climate%20Pledge%20now%20has%20over%20500%20signatories