2024.12.10:Supercharge Digital Transformation by Consolidating CAD to NX (Commentary)
Key Takeaways
- Mechanical CAD data migration has been a very difficult problem for decades.
- MultiCAD support is needed sometimes, but a single CAD solution is much more efficient and effective.
- CAD data is foundational to digital transformation improvements, and using multiple CAD solutions adds complexity, cost, and risk to product design and realization processes.
- The Siemens Content Migration Manager for CAD Solutions (CMM) enhances NX’s utility by maximizing the transfer of design intelligence from legacy CAD data to support the reuse of CAD models, drawings, and designs, thereby enriching the digital transformation initiative.
Introduction
Engineers have been using mechanical CAD software for over 50 years to develop product designs. Techniques have evolved from 2D wireframe to parametric 3D models during the first 30 years, and over the past 20 or so years, capabilities have been extended and optimizations implemented. Current modeling kernels can create virtually any shape, addressing issues that vexed developers for years, such as slivers, disappearing edges, intermediate non-manifold situations, and other degeneracies. Capabilities added more recently include product manufacturing information (PMI), modeling structures to support additive manufacturing, process-specific features, style surfacing, and assembly modeling advances.[1]
The competition among CAD solution providers over the years has been extraordinary, which is why we have the impressive capabilities that exist today. The downside is that, by definition, standards don’t exist for innovation, so advances from one solution provider are often not directly compatible with a competitor’s data structures and methods. CAD veterans have used various tools such as IGES, the suite of STEP protocols, direct translators, and alternative techniques that leave data in its native or B-REP format in the target solution, resulting in the loss of CAD model intelligence. Each tool and technique has pros and cons.
MultiCAD, when engineers collaborate using different CAD solutions to develop a product, is a common practice in all but the most disciplined or siloed businesses. The main reasons for multiCAD include:
- Supply chain—requiring suppliers to use the same tools as an OEM adds cost.
- Adopt new solution, don’t retire old—Since data migration takes time and can be error-prone, legacy software is kept running, hopefully in a read-only mode.
- M&A—often reducing the promised synergy benefits.
Working in a single CAD environment is more efficient, due to the economy of scale and duplication elimination. While the cost of migrating affects the ROI early, data can be fully utilized, and costs can be minimized, including licensing, training, support, integration, and process complexity improving the return over time. Furthermore, advanced software features can be leveraged to improve efficiency and innovation further.
MultiCAD Issues
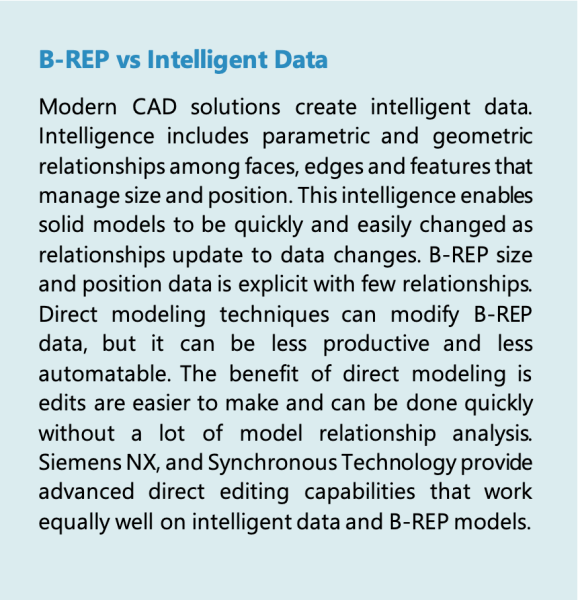
While multiCAD can work with stable geometry, that is, geometry that can be represented as a B-REP, with no changes required (e.g., interface zones, standard or purchased parts that should not be modified), data management is still complex. Besides those limited use cases, geometry is modified during product development and sustainment. A critical question is “where is the master released data stored?” Is it in a single PLM environment? If so, then the data management solution becomes more complex with integrations and translations, or even a second PLM, which makes for more complex, often custom integrations to keep data synchronized and support release dependencies. When more repositories exist, processes such as change, release, and search become more complex, and time is wasted verifying that correct data has been found.
When collaboration needs to happen at the model level (i.e., multiple engineers modifying the same models), employing a multiCAD strategy is too cumbersome to support fluid collaboration. For example, moving a hole pattern change from one model to a related model in a different CAD solution takes extra processing time. Other issues with translation software include feature mapping mismatches, loss of intelligence in the models, and breaking of downstream links to drawings, machining tool paths, associative simulations, and other critical capabilities. Things that just work in a homogeneous environment require customization and complex workarounds.
People or organizational issues also abound in multiCAD environments. There are never enough resources in enterprises or project teams to support multiple CAD tools. CAD applications are complex, and while at a basic level, it’s easy to move back and forth between tools, leveraging the advanced capabilities that modern tools have to maximize productivity requires expertise and comes from continuous use and study. Learning and maintaining expertise in two or more CAD tools that do the same thing is not a good use of time and having to maintain multiple skill pools adds complexity and guarantees scheduling conflicts. Finally, people generally don’t like change, and engineers often resist changing tools.
Using a single CAD solution eliminates these issues, and when combined with common processes across work teams, real efficiency happens, the software is used to its maximum potential, and the digital transformation delivers more of what was promised.
Siemens Xcelerator
Siemens Xcelerator is a comprehensive digital business platform designed to accelerate digital transformation for companies of all sizes. CIMdata has written a lot about Xcelerator,[2] and we believe it is a best-in-class platform that can solve most industrial business challenges. Siemens’ offerings within the mechanical design domain include NX™ software, their CAD solution, and Teamcenter® software, their PLM solution. Both are used across industries, from the very largest to startups, and have proven to be able to develop and manage the product information needed by companies to be successful.
NX Content Migration Framework
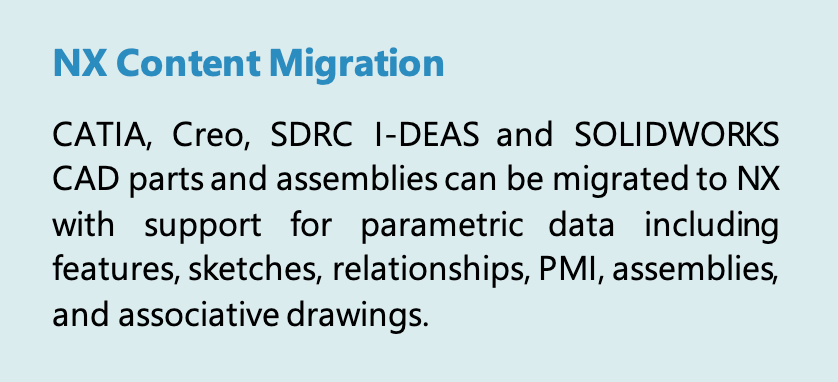
One of the gems within Xcelerator and the Siemens organization is Content Migration Manager for CAD (CMM) solutions. This software application and optional service component is able to migrate CAD data from CATIA, Creo, SOLIDWORKS, and others into native NX files with parametric features, relationships, PMI, and associative drawings intact. Support for these objects enables legacy data and designs to be properly modified using Siemens NX while maintaining design, data, and configuration integrity.
The application is configurable and can support bulk or on-demand migration. Migration can support B-REP or parametric/history-based data. B-REP translations process faster and are appropriate for geometry that will not change, such as standard or purchased parts. Furthermore, NX Synchronous Technology enables fast editing for a wide variety of geometric modeling techniques when the customer’s design intent, further re-use, and engineering change require it.
Parametric data is translated using a recipe approach. The legacy data’s history tree is analyzed and transformed into a recipe that gets executed by NX. While conceptually straightforward, the complexity is in the detail, as every solid modeling kernel has unique algorithms, features, and data structures. Common discrepancies include special features that don’t map to NX, small object tolerances, sliver surfaces, gaps between surfaces, and intermediate non-manifold geometric situations. Recipes are optimized to successfully generate parametric data, but when a failure happens, the process fails gracefully, retains what was successfully translated, and brings in the remaining geometry as B-REP. Drawings, including views, dimensions, and annotations, are migrated and update when their parent 3D models are modified.
Teamcenter is an optional solution that can be included in the migration. Metadata from the legacy PDM/PLM solution can be transferred into Teamcenter and associated with the migrated CAD models, assemblies, and drawings. CMM and migration assistance can be delivered as a service from Siemens or licensed and installed for on-demand use, giving the company’s flexibility in how to execute its migration. Additionally, Teamcenter is not required, and the framework can read and write directly from a file system, enabling companies to do what they wish with the resulting data.
Getting Started
To get started on the decision to migrate to NX, Siemens offers an assessment process. They execute an analysis tool on the prospect’s data and generate reports to identify the source CAD capabilities used and forecast the expected results from a migration. Sample migrated data can be provided, enabling the company to better understand the quality of data it will receive. According to Siemens, well over 90% of the source CAD capabilities are supported. CIMdata also published a white paper describing Siemens CMM in more detail.
Conclusion
MultiCAD has been a reality for many years and will continue to be for the foreseeable future. While there are good reasons to enable and support a multiCAD environment, it does take more resources, adds complexity to product development processes, and reduces the effectiveness of digital transformation programs.
Content Migration Manager for CAD Solutions from Siemens enables migration of complex parametric, history-based parts, assemblies, and associative drawings from CATIA, Creo, SDRC I-DEAS, and SOLIDWORKS to NX with intelligence intact. This is a big deal, as recreating parametric data and associative drawings can take a lot of time, impacting budgets and schedules. If you are considering a replacement CAD solution or are using NX in a multiCAD environment, contact Siemens to learn how you can consolidate onto NX and other Siemens products to improve the effectiveness of your digital transformation.
[1] Research for this paper was partially supported by Siemens Digital Industries Software.
[2] https://www.cimdata.com/en/resources/solution-provider-profiles/plm-dossier-siemens-plm-software