2024.11.7:Battery Engineering and Mass Production Need Integrated Digital Solutions (Commentary)
Hexagon Integrates Multi-Discipline Battery Physics with Manufacturing
Key Takeaways
- Companies need new, robust digital solutions that enable the design, packaging, and manufacturing of the latest innovative battery subsystems.
- New battery technologies are emerging and evolving faster due to improved understanding as innovative options are assessed using advanced simulations.
- Hexagon provides simulation capabilities that leverage electrochemistry, physics, and test data, designed to aid battery engineers to innovate across all physics, from anode and cathode details to final battery packaging into products.
- Hexagon also provides virtual manufacturing, inspection, and calibration solutions that accelerate manufacturing and reduce scrap rates.
- Furthermore, Hexagon provides state-of-the-art gigafactory digitalization and visualization to help optimize agile manufacturing planning and operations required by the accelerated development of battery products while assuring sustainability and traceability criteria remain visible.
Challenges Facing Battery Engineering
Batteries provide energy storage for complex products, from cell phones to electric vehicles (EVs) and short flight aircraft to buildings that need sustainable and reliable energy supplies. Battery engineering challenges include energy density, reliability, power density, safety, mass production, and learning for usage experience. Charging and discharging dynamics affect battery performance, durability, and safety that needs multi-disciplinary simulation and data collection to accelerate learnings. Battery pack and cell energy storage options are multiplying as investment is focused on improving energy and power density—the amount of energy stored in a specific weight or volume.[1]
Charging and discharging dynamics need to be balanced with electrode’s electrochemistry, degradation, cooling capability, and safety. New materials and innovative manufacturing processes are needed to lower system costs. Sustainability as a core principle requires that manufacturing processes as well as factory infrastructure are optimized using trusted simulations to accelerate innovation realization and enable reduced lifecycle wastage. Merging measurements from shopfloor inspections with validation results as mass production proceeds provides product and production quality insights that identify upgrades in battery design and manufacturing. The future of battery manufacturing is smart, connected, and autonomous; it requires advanced digital ecosystems to keep a company competitive.
Hexagon is aware and is addressing the needs of today’s battery designers and manufacturers as they have summarized in The following list:
- Designing electrodes with the correct anode/cathode chemistry while considering morphological aspects requires significant investment.
- Evaluating cell performance and identifying degradation risks in the absence of physical prototypes is a significant challenge.
- Assessing the mechanical properties of a jelly-roll or stack configuration without prototyping is highly challenging.
- Determining the most effective cooling system to optimize battery performance requires significant resources when relying on a trial-and-error approach.
- Ensuring battery safety and developing fail-safe designs with effective mitigation strategies is critical.
- Integrating the battery into powertrain evaluations to ensure sufficient power for vehicle use cases presents additional complexities.
Hexagon Battery Design & Engineering Solutions
Hexagon tackles the challenges of traditional trial-and-error battery material exploration with advanced electrode-domain simulation technology. By utilizing either CT scans or synthetically created morphologies, engineers can gain microscale insights through electro-chemical simulations. The solution integrates an advanced electrochemical model developed by the renowned research institute Fraunhofer ITWM to solve thermo-electrochemical equations based on these realistic microstructures, predicting the impact of manufacturing processes on cell behavior and uncovering local degradation mechanisms. It also provides a tool for estimating the mechanical properties of jelly roll/stack materials through microscale-based structural analysis using the Representative Volume Element (RVE) modeling technique. Virtual testing of the constructed RVE simplifies estimation of macroscopic mechanical responses, thereby streamlining the process of macroscale battery structure analysis. Figure 1 summarizes the steps involved that improve battery dynamics understanding leading to optimal designs found through virtual exploration.
Figure 1—CT Scan Import to Optimize Battery Components Design
(Courtesy of Hexagon)
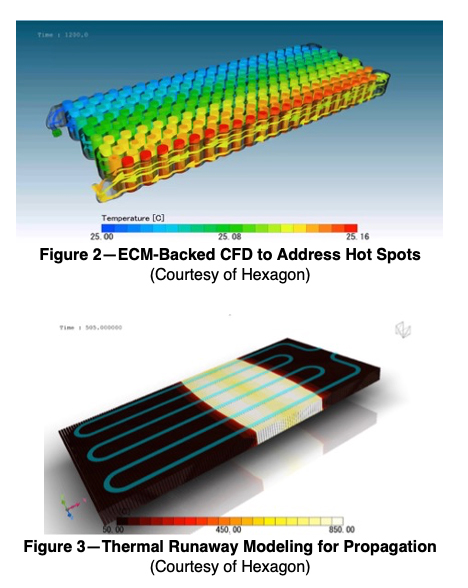
Next, at the battery pack level, design needs to consider cell electrochemical response, environmental conditions, load profiles, and safety. Engineers need efficient modeling tools to access this understanding and conduct trade-off studies. Hexagon provides essential tools to support engineers in achieving their goals with two approaches for CFD: (1) the equivalent circuit model, ECM (Figure 2) and (2) the physics-based electrochemical model. Additionally, the ability to import third-party cell models allows engineers to fine tune their virtual models. For robust design of battery products, Hexagon’s thermal runaway simulation technology, shown in Figure 3 offers an efficient workflow with minimal computational load, greatly enhancing the productivity of the design process. Engineers can quickly evaluate the safety of battery products against thermal runaway during the design phase, eliminating the need for prototyping and ensuring the product meets safety expectations.
Hexagon Battery Manufacturing Solutions
Hexagon Virtual manufacturing solutions help to optimize designs by showing the impact of the process on the product e.g., residual stress leading to potential mechanical failure. They also help reduce physical trials tests, consequently lowering costs by simulating the optimal process to accelerate manufacturing operations like laser welding. Hexagon’s Semi-Automated Separator film inspection machines, powered by AI-based visual defect detection, help with incoming goods inspection. There are also solutions that inspect installation and calibration of production machines to avoid any deviation.
Figure 4—Hexagon’s Manufacturing Inspection Automation Equipment
(Courtesy of Hexagon)
To enable production scaleup while maintaining high-quality standards, Hexagon has introduced PRESTO, an automated and agile end-to-end package that streamlines the inspection of hundreds of battery trays daily for instance while relying on a patented shiny surface laser scanner, shown in Figure 4.
Figure 5 summarizes Hexagon’s CT scan analysis for non-destructive inspection, allowing early detection of potential defects such as delamination, welding inclusions, or anode/cathode overhangs. This technology facilitates early quality assessment powered by Machine Learning (ML) based picture segmentation for improved accuracy.
Figure 5—CT Scan Analysis Enables NDE
(Courtesy of Hexagon)
Hexagon Sustainable Digital Solutions for Battery Gigafactories
Central to Hexagon’s strategy is the implementation of enterprise Quality Management Systems (QMS), fostering full data traceability, predictive quality, and connectivity from the shop floor to the top floor. This sustainable digitalization effort is critical not just for maintaining high standards of quality control at each production step but also for ensuring compliance with future environmental regulations. By monitoring data, product, and process quality, Hexagon’s QMS solutions contribute to the larger goal of delivering greener batteries, essential for a sustainable future. By combining advanced metrology, automated inspection, non-destructive testing, and a forward-thinking QMS, Hexagon empowers battery manufacturers to achieve scalability, sustainability, and profitable innovation. Hexagon’s gigafactory digitalization and optimization solutions stand at the confluence of real and virtual worlds, pioneering a smart digital reality that harnesses the power of digital twins. These intricate digital replicas capture every aspect of the gigafactory—from the granular details of the production line to broader operational workflows. It uses state-of-the-art Hexagon geosystems sensors to capture factory reality and combines this data with 3D models to enable visualization and analysis for decision making. Figure 6 gives an example of data measurements and data traceability within a gigafactory.
Figure 6—Quality Management Solution Within a Gigafactory Helps with Data Traceability
(Courtesy of Hexagon)
This suite of solutions from engineering to quality inspection leverage the power of AI for use cases that accelerate the innovation cycle—accurately simulating physical phenomena that improves quality by preventing defects—moving key product decisions to earlier in development. By understanding the function and features earlier in development, repair cycles are eliminated lowering scrap during development and manufacturing mass production. Figure 7 highlights what is possible during design, manufacturing, and inspection.
Figure 7—Artificial Intelligence Improves Design, Manufacturing, and Inspection
(Courtesy of Hexagon)
Conclusion
Hexagon’s suite of simulation, manufacturing, and gigafactory visualization solutions provides a foundation to address the needs of battery manufacturers as the competitive environment intensifies. At the 2024 Battery and EV Show recently held in Detroit, Hexagon demonstrated these capabilities to many interested engineers and managers. Keynotes and panels during the show emphasized the need for faster, agile processes which allow OEMs and their battery suppliers to quickly adjust their battery architectures and related manufacturing as the EV market changes. CIMdata believes that companies that stay agile as battery technologies evolve should be able to realize significant productivity benefits when using Hexagon’s suite of solutions.
By establishing primary themes for their broad battery solution set, see Figure 8, Hexagon provides simulation that improves coupled-physics understanding, plan manufacturing virtually, and manage the gigafactory with some of the best inspection technologies tied into their growing AI/ML capabilities. CIMdata has seen the breadth of Hexagon’s solutions across the key disciplines that will lead battery energy storage engineering for stationary and mobility products. Agile manufacturing becomes the best practice as virtual engineering techniques are applied.
Figure 8—Hexagon’s Primary Themes
(Courtesy of Hexagon)
Hexagon, a proven leading solution provider, builds on their strengths as they enhance their solutions across simulation, inspection, gigafactory modeling and visualization and now AI/ML. CIMdata recommends that companies looking to improve their battery engineering and manufacturing agility include Hexagon solutions in their evaluations.
[1] Research for this paper was partially supported by Hexagon.