2024.9.3:Enhancing Quality Management with Autodesk Cloud PLM (Commentary)
Closed-loop quality management within Autodesk Fusion Manage
Key Takeaways
- As product complexity increases, quality and reliability have become two of the most important considerations for companies today since the cost of poor quality directly impacts an organization’s profitability and customer loyalty.
- Too often companies design in isolation, disconnected from manufacturing, supply chain, service, and other downstream functions. With little to no feedback during early design, the result is higher defect rates. When quality defects are not identified and corrected early, the cost of failure rises as the product moves further through its lifecycle.
- A strong quality management solution must be a closed-loop process combined with engineering change management that enables stakeholders across the organization to participate. It must be flexible and adaptable to meet the needs of a growing business.
- Autodesk Fusion Manage includes a comprehensive quality management solution as part of its cloud PLM solution with extensive quality capabilities all linked to the appropriate data (i.e., parts, BOMs, specifications, etc.) and driven under change control to ensure closed-loop quality.
Introduction
The concept of quality is often narrowly focused on reducing defects in manufacturing, but quality affects every aspect of a company and its success. To truly excel, quality should be everyone’s responsibility, with all employees involved in identifying and playing a role in solving quality issues. This collaborative effort across different functions and levels within an organization is essential to ensure that quality is designed into every product from the outset.[1]
The increasing complexity of products makes quality and reliability critical considerations as the cost of quality directly impacts profitability. Today’s smart, connected products require manufacturers to be more agile—developing products that balance hardware and software functions, manage diverse options across the supply chain, and meet increasing customer demands for personalized options. These pressures require manufacturers to adopt a more systematic approach to managing quality while remaining flexible enough to meet rapidly evolving market needs.
Defects and failures lead to costly scrap, rework, recalls, and increased warranty claims. Quality issues downstream, whether in the supply chain or with customers, decrease productivity by diverting some of a company’s best resources from essential work to resolve these issues in the field. Often, multiple resources from different functions get involved, further reducing efficiency. The lack of a connected quality management and Product Lifecycle Management (PLM) solution can delay time-to-market and reduce customer satisfaction and brand reputation—all negatively impacting profits and revenue.
Addressing quality issues early leads to more sustainable practices by reducing waste and improving resource efficiency. However, companies often develop products in isolation, disconnected from manufacturing, supply chain, service, and other downstream functions, resulting in higher defect rates. If quality defects are not identified early through verification tests, conformance to quality requirements, inspection plans, and other means, the cost of poor-quality rises as the product progresses through its lifecycle.
A solution that enables a company to address quality holistically is essential. This involves not only identifying nonconformance and root causes but also leads to continuous improvement across the organization. High quality is a key differentiator in competitive markets, attracting and retaining customers while strengthening brand reputation. Strong closed-loop quality management combined with enterprise-wide change management is fundamental to long-term business success. What is required is a comprehensive PLM solution with closed-loop quality management. When quality management is combined with engineering change management, it facilitates collaboration across the organization, including manufacturing, sourcing, supply chain, service, sales, warranty, and other functions.
Autodesk Quality Management Solution
Autodesk Fusion Manage is a robust cloud PLM solution with enterprise-wide change management seamlessly integrated with quality management, all built on Autodesk Fusion, the Autodesk industry cloud for manufacturing. By combining both quality management and change management into a series of closed-loop processes, Fusion Manage provides a strong solution that improves design, identifies supplier issues, and enables finding the root causes of failure faster. As a result, quality products can be brought to market more quickly.
Autodesk quality management employs standard quality artifacts from academia and industry that are easy to adopt and designed to work together, encouraging best practices. These out-of-the-box (OOTB capabilities are easily configured and compatible with various other quality artifacts. Non-conformances (NC) can be linked to affected items and related images, driving corrective actions through comprehensive incident reporting, analysis, and disposition workflows. Once a NC is reviewed, a corrective and preventative action (CAPA) can be created automatically, defining tasks to measure, analyze, and address the NC.
The CAPA improvement process can automatically initiate an engineering change request (ECR), making both quality and change management processes more efficient. ECRs can then be reviewed, and if appropriate, an engineering change order (ECO) can be created to control design changes to the non-conforming items, ensuring updates, approvals, documented releases, and revised items. Fusion Manage provides extensive enterprise-wide change management, controlling communication of changes, requirements, test procedures, and manufacturing controls in a closed-loop series of configurable workflows that connect quality processes and data with product development processes across the extended enterprise as shown in Figure 1.
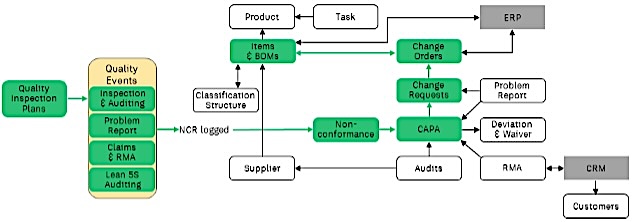
(Courtesy of Autodesk)
Autodesk quality management handles multiple stakeholders’ needs by offering templates for various quality processes. For instance, a user can run a first article inspection as part of a Quality Inspection Plan. If the plan fails, an NC is automatically created using templates that enable various stakeholders to assist with quality and report non-conformances. The solution also includes the ability to create a Failure Mode and Effects Analysis (FMEA) to identify, manage, and verify processes. This enables flexible scoring on failure modes for each type of functional design or process analysis, facilitating continuous improvement and compliance.
Supplier performance and quality are tracked with supplier corrective action requests (SCARs). Supplier auditing can occur before onboarding and after at configurable frequencies, with the audit documentation stored in Fusion Manage. This can potentially drive an additional CAPA for the supplier to regain compliance. Other quality processes included are control inspection plans, equipment maintenance, audit maintenance, test equipment maintenance, supplier quality business review (SQBR) reports, claims management, warranty management processes, and more—all of which can be easily configured to meet an organization’s unique business needs. Secondary quality processes such as CE Marking, 5S Auditing, 8D reporting, employee training, and equipment calibration are also supported.
Compliance and reliability are key aspects of a quality control program. Autodesk provides traceability on specific quality issues across the lifecycle, maintaining a history of issues, corrective actions, and electronic signatures meeting auditor requirements. Configurable OOTB dashboards and reports offer real-time insights on product quality, defects, and change orders. Reports can also be created using external business intelligence tools for data integration across other enterprise applications.
Fusion Manage can be configured for industry-specific quality processes such as Advanced Product Quality Planning (APQP) and Production Part Approval Process (PPAP) for the automotive industry. Its flexible workspaces and workflow-building utility enable the digitization of nearly any quality process in a robust cloud PLM solution, eliminating collaboration barriers that typically hold companies back.
Continuous Improvement and Importance of Flexibility
Continuous improvement of products and processes is fundamental to an effective quality management program. Organizations constantly face unexpected changes and new complexities, making the ability to continuously adapt essential. To meet the needs of an extended enterprise, a flexible and open PLM solution with embedded quality management capabilities is crucial. This ensures that not only are products manufactured efficiently, but agile product development processes can grow and adapt to keep pace with business evolution, including access for all suppliers.
To achieve this, a quality management solution embedded within a flexible, open cloud PLM solution is indispensable. Autodesk quality management leverages OOTB quality artifacts to encourage best practices and automates the collection of data in various formats,, such as CAD files, documents, spreadsheets, presentations, reports, and test data, that are linked to various quality and change management processes. This facilitates efficient quality-related workflows and enables organizations to pivot and adapt processes as needed without sacrificing quality.
Autodesk accomplishes this by placing data at the center of the solution. Related business data—ideas, requirements, specifications, designs, tests, analyses, and more—are all managed within the same system as the artifacts and processes. This centralization ensures that data is linked exactly where needed, maximizing efficiency. Autodesk quality management offers the flexibility to configure fields, records, relationships, and business processes, enabling the implementation of high-value processes that maximize ROI.
Fusion Manage provides a robust reporting framework that produces real-time KPIs and insights, driving timely, data-driven decisions enabling the ability to continuously improve. As a cloud-based solution, Fusion Manage scales easily with different subscription options, along with offering flexible access to suppliers. Fusion Manage is based on an open API, providing integration technology that maximizes connections between domains such as CRM, ERP, MRP, and MES. This integration capability ensures that all aspects of the business are connected and aligned, fostering a holistic approach to quality management and continuous improvement.
Conclusion
Autodesk Fusion Manage with quality management provides a comprehensive cloud PLM solution that addresses the quality and collaboration challenges faced by many organizations. By combining industry-accepted best practices with flexible closed-loop quality management and PLM engineering change management, Fusion Manage forms a robust and holistic quality solution. CIMdata believes companies can realize significant improvements in their cost of quality by leveraging Fusion Manage, highlighting its potential for impactful operational enhancements.
CIMdata is impressed with the extensive quality management capabilities within Fusion Manage that place product data at the center of the quality and change management closed-loop processes. This ensures that all relevant information is integrated and accessible and facilitates seamless collaboration and efficient quality management, making it easier to maintain high standards and quickly adapt to unforeseen changes.
Fusion Manage has successfully integrated industry-accepted best practices with a flexible closed-loop quality management system, creating a comprehensive quality solution. CIMdata is pleased to see a solution that combines the best of quality management with a flexible cloud-based PLM solution that can meet a company’s current and future needs. Regardless of company size, this adaptability ensures that organizations can continue to benefit from Fusion Manage as their operations evolve and grow. The solution not only addresses an organization’s immediate quality and collaboration challenges but has the potential to support long-term growth, continuous improvement, profitability, and customer loyalty.
Given these advantages, CIMdata recommends that companies aiming to improve their quality management include Autodesk Fusion Manage with its quality management capabilities in any evaluation of potential solutions.
[1] Research for this paper was partially supported by Autodesk.