2024.4.2: Broad Approach to Quality and Compliance Management (Commentary)
Key Takeaways
- As product complexity increases, organizations need quality and compliance management techniques applied across the complete lifecycle–this requires organizations to refine roles and governance within PLM in the context of product lifecycle quality.
- Quality Management Systems (QMS) must expand beyond a narrow focus of managing manufacturing repeatability and customer usage complaints.
- Exploring quality from the very start of a new idea, in the context of a trusted digital twin while comprehending sustainability requirements, changing consumer usage patterns, and evolving manufacturing practices, will be the hallmark of leading products companies.
- Siemens Xcelerator enables the digital thread and management of product data flowing across the complete lifecycle supporting closed-loop quality and comprehensive digital twins both on premises and on the cloud.
- Siemens continues to enhance their QMS solutions, such as Teamcenter Quality, with capabilities for lifecycle collaboration defining and managing a Bill of Quality.
Introduction
CIMdata’s definition of PLM emphasizes the complete lifecycle of a product and all its related data and processes, from idea inception to requirements definition, to planning and development, with supply chains, and then mass production and actual in-service performance and product upgrades. Quality Management Systems (QMS) have historically focused on manufacturing products consistently and improving product durability and reliability. Imagine applying QMS practices across all aspects of an organization developing and operating products. The techniques of quality management can be applied to engineering processes, manufacturing processes, supplier processes, and even discoveries in new markets. Using QMS systems has improved as PLM systems have enabled an accurate digital twin throughout the lifecycle.[1]
As product complexity increases with new and expanded features being delivered while a product is in-service, a more expansive use of quality analysis methods and practices is needed. This comprehensive quality management paradigm assures product quality always earns the trust of customers, rewarding the manufacturer with higher sales volumes and brand loyalty. This is broader than the notion of classical quality management systems using their own process and data silo applying statistical process control as though every manufactured item is a black box to be studied as a population of samples.
Siemens introduced Teamcenter Quality in 2021 to expand QMS capabilities, summarized in a CIMdata Commentary with a testimonial from Dana Corporation.[2] Siemens Teamcenter Quality with its new Customer Zero Process is a complete lifecycle quality management ecosystem built on Siemens Xcelerator. The inaugural usage of the Customer Zero Process was within Siemens AG business units, improving their own manufacturing and service quality management across product lifecycles.
Quality Management Responsibilities Expand
Competitive and product complexity pressures require faster decisions made well. Systems engineering, Design for Six Sigma (DFSS), and design thinking are skills practicing engineers must embrace, regardless of their domain of expertise. Product requirements are best managed in a repository containing the authoritative truth that enables different views and analyses as product lines are conceived and enhanced. Modern PLM ecosystems, like Siemens Xcelerator, are well positioned to foster a quality management environment throughout a product’s lifecycle. Applying systems engineering principles everywhere in the lifecycle requires a quality management mindset where anomalies uncovered in FMEA, inspections, or complaints can be immediately evaluated with models. This applies to quality for newly discovered customer usages.
There are many stakeholders who provide insights and knowledge when assuring a product’s quality. Siemens involved their own internal broad set of stakeholders to understand how these stakeholders want to effectively interact. Siemens businesses and service functions act as the first customer to test the end-to-end customer experience of Siemens products, as shown Figure 1.

(Courtesy of Siemens)
At Siemens’ Realize LIVE Europe 2023 conference, Mr. Karim Gharbi, IT Project Manager and Enterprise Architect at Siemens Digital Industries Software, gave an insightful presentation on how collaboration within the company enables greatly improved solutions. To improve collaboration, the “Customer Zero approach” relies on collaboration across different Siemens Digital Industries Software departments from software development through operations and factory automation. He discussed how a broader quality management framework with effective data governance enables collaboration between various roles during each product lifecycle phase: planning, development, manufacturing, and service.
To support this vision, a digital twin must be available on demand and accurate to the latest customer usage patterns. Many work items about a product have traditionally been managed in separate IT systems, often with bespoke user interfaces tuned for authors, not readers and researchers. A digital transformation is needed to connect these work items efficiently enabled by consistent product terminology. Digital twins are the technology to bring work items into proper context for ongoing engineering and quality work. Virtual quality assessments can now include variation and simulation analyses (VSA). When models are digitally validated with actual coordinated-measuring machines inspections, they can be used to confirm appropriate programing as part of dimensional planning and validation. The designer can interactively see the effect of design choices on manufacturing’s inspection Bill of Process (BoP). Thus, quality management becomes a closed loop.
A closed-loop quality approach enables variation analysis that is digitally validated employing simulation earlier in the product development process. Creating and sustaining an actionable, living digital twin annotated with failure insights and design/supplier weaknesses improves product quality management. Containment as well as preventive measures then become a pervasive, even predictive, part of the engineering, manufacturing, and customer service processes. The digital twin is used more and more to assess operational anomalies to understand whether an emerging field issue might be the bud of a quality problem. By using a digital twin, even supply chain improvements can be immediate when integrated quality management practices are applied.
Enhancing Lifecycle Value
Siemens Teamcenter Quality is designed to help customers bridge gaps between roles and work elements improving collaboration. Siemens recognizes that quality and compliance management’s value must extended beyond production to all core business processes for all product domains. Siemens’ quality strategy incorporates a comprehensive closed-loop vision across these multiple domains and their disciplines shown in Figure 2.

(Courtesy of Siemens)
This means breaking down diverse data silos (and supporting organizational re-engineering), providing a capable and flexible work items repository improving complexity management, data sharing, and configuration management.
Figure 3 illustrates an extended architectural landscape to encourage Closed-Loop Quality, including ERP, PLM, and MES systems applying artificial intelligence using machine learning (AI/ML). Note how the diverse roles interact using the digital twin, which is elaborated with quality specifications and measures throughout the lifecycle.

(Courtesy of Siemens)
Teamcenter Quality utilizes Siemens Xcelerator to provide a product lifecycle collaboration backbone. As part of the solution portfolio, artificial intelligence and machine learning (AI/ML) enable a new application named Insights Hub Quality Prediction. It is designed to improve quality, throughput, and cost efficiency by applying ML algorithms. An AI/ML empowered closed-loop quality approach broadens the domain of quality and compliance management to the complete closed-loop lifecycle of products.
Accelerating Learning Cycles
A greater focus on the continuous feedback loop, as taught by Dr. Edward Deming, is related to the usage of Kaizen Plan-Do-Check-Act (PDCA).[3] Learning and feedback to proactively repair and enhance products is driven with the Plan-Do-Check-Act learning cycles. An annotated digital twin provides context of the insights making Planning easier. Do & Check occur interactively with the digital twin allowing Act to quickly proceed.
To address the master data integration challenges Siemens’ holistic vision for quality management systems has adopted the PDCA paradigm, applying it to connect key work elements of the product in the context of discovery with applied lessons from ongoing experiences. The cycles are repeated until a solution is found and can traverse to early work products wherever the problematic conditions started.
Data integration across formerly siloed applications is a key to success for streamlining quality management and keeping it “closed loop” with continuous, contextual feedback encouraging a culture of quality within a company’s value streams. Configuration and change collaboration within this continuous feedback loop enables full traceability, making quality management more proactive than reactive, and thus much faster. This leads to a holistic view of quality management rather than just a mass production manufacturing view.
This broader quality management environment improves systems designs over their entire lifecycle, making sure products placed in initial service perform better as they are upgraded. This is accomplished when leveraging digital twins and digital thread insights. Figure 4 illustrates how Siemens integrates the quality domains encouraging a holistic product quality view.

(Courtesy of Siemens)
A closed-loop quality approach allows companies to leverage the power of the digital twin to continuously improve quality control processes. It helps simulate design and production processes to sort out quality problems in the virtual realm that would otherwise not be discovered until reaching the production stage on the shop floor. Interconnecting disciplines and domains help shift the quality mindset to one in which learned insights build trust continuously across the life cycle. As new field / phenomena results are captured, models and their simulations are improved, and quality risks and learnings are explored. It incorporates lessons continuously through improvements learned effectively.
Conclusion
Siemens’ Quality Management Solution, Teamcenter Quality, provides a foundation to address the quality data integration and collaboration challenges with complex products. CIMdata forecasts that companies connecting data effectively should be able to realize significant productivity benefits using Siemens Teamcenter Quality management solution.[4]
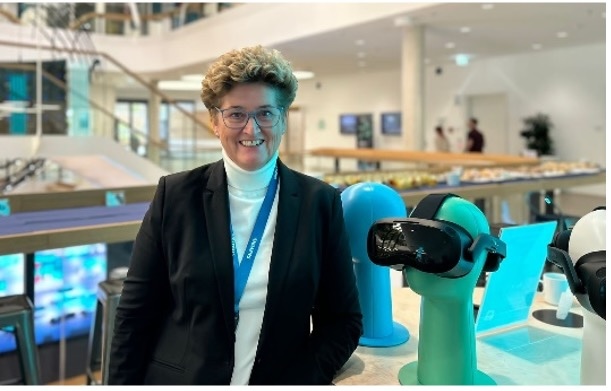
Setting a vision with their expanded Quality Management solution, Siemens themselves derives benefits. Ms. Monika Hofrichter, Global Head of Quality Management and EHS at Siemens Digital Industries, states “We use what we sell—with our Customer Zero approach, we can incorporate our own expertise in the optimization and standardization of our quality processes into the Siemens software application Teamcenter Quality and thus make it usable for our customers and ourselves. A major advantage is that we can use the product data for the quality methods from our PLM environment at any time.” CIMdata is glad to see the broader Siemens influence when using their PLM solutions for agile manufacturing, energy, and medical products. Leaders use their own solutions, just as CIMdata expected Siemens would.
Siemens Xcelerator platform with Teamcenter as the collaboration and data management backbone enables customers to accelerate learning and enhancement cycles. Holistic quality management encourages linkages between silos of experts and their knowledge, driven by the latest measurements. This is what happens when Siemens, a proven leading solution provider, builds on their industrial strengths as they enhance their PLM and quality management solutions. CIMdata recommends that companies looking to improve their quality management systems include Siemens’ Teamcenter Quality, with its Customer Zero approach, in their evaluation of potential solutions.
[1] Research for this commentary was partially supported by Siemens.
[2]https://www.cimdata.com/en/resources/complimentary-reports-research/commentaries/item/16341-a-broad-approach-to-quality-management-commentary
[3]https://en.wikipedia.org/wiki/PDCA
[4]https://www.sw.siemens.com/en-US/siemens-quality-management-in-the-digital-era/