2024.1.30:Smart Manufacturing – Critical for Success in Today’s Complex Heavy Equipment Industry (Commentary)
Key Takeaways
- Increasingly, heavy equipment manufacturers must produce custom configurations, often in small quantities, while simultaneously managing increasing product complexity―leveraging closed loop smart manufacturing is required to compete and win in today’s complex heavy equipment industry.
- Smart manufacturing requires effective collaboration among product engineering, manufacturing planning, production, and service operations.
- A comprehensive smart, collaborative manufacturing environment is essential to analyze the impact of a product mix on production, allowing companies to optimize overall throughput.
- Siemens Xcelerator from Siemens Digital Industries Software, an open digital business platform to accelerate digital transformation and value creation has been tailored to deliver a smart manufacturing environment for heavy equipment industry competitors.
Introduction
Heavy Equipment manufacturers make highly configured products in low production volumes. Their margins are tight. Every opportunity to make savings is critical. Manufacturing efficiency can make a significant difference, with massive impact on profit. Additionally, trends like electrification, digital capabilities, and customers specializing in unique operations add complexity by multiplying the number and variety of components, suppliers, and customization requests.[1]
These manufacturers are being challenged by their customers, the competition, and government regulators, to develop smarter, more eco-friendly equipment in an increasingly difficult economic climate. Key challenges include tougher emissions standards, higher performance requirements, ever-increasing safety standards, electrification, and the application of new technologies such as augmented reality and artificial intelligence. Additionally, companies realize the safest place for their operators is outside the mine or construction site, so remote teleoperation and autonomy are often sold as a safety asset.
As a result, heavy equipment is getting smarter. Much of today’s equipment is software- and electronics-driven, can connect with other machines and systems, and is able to operate autonomously. Manufacturers have a fundamental requirement to manage the rapidly increasing complexity of hardware, software, and electronics integration within heavy equipment to drive product development, product performance, and differentiation. To do this, competitors in the heavy equipment industry must create smart manufacturing environments that enable them to ensure compliance, quickly introduce new, complex products, deliver higher manufacturing efficiencies, and achieve expected quality regardless of production volumes.
Further, customer demands for “personalized” products increase product and process complexity of both development and production as well as long-term service. Manufacturers need highly flexible integrated information flows and processes that can adapt to product and market changes. Implementing integrated Manufacturing Enterprise Innovation Platforms[2] can help achieve faster ramp-up to production and reduced time to market, while improving response to changes in customer demand.
CIMdata believes that heavy equipment manufacturers who address these issues will position themselves to more quickly deliver the complex Configure-To-Order (CTO) products their customers are demanding, make more efficient use of their manufacturing facilities and service resources, improve their competitive position, and increase customer loyalty.
Efficiently Producing Complex Products
To efficiently realize global design and production, manufacturing enterprises must design, manufacture, and service multiple configurations and variants of a product family in a cost-effective manner. This means:
- Establishing a comprehensive digital thread that enables multi-domain collaboration and re-use and leverages common information from design to execution and beyond.
- Establishing best practices for complexity management―enabling design anywhere, build anywhere for complex CTO equipment.
- Creating a closed-loop manufacturing (CLM) environment that enables direct cross-domain (PLM/ERP/MES) feedback loops to support smart manufacturing.
CLM enables managing changes between engineering and manufacturing (and service) and incorporating feedback from the shop floor. Built on seamless integration between PLM, ERP, and MES, CLM enables synchronization and optimization along the entire value chain. It supports direct cross-domain feedback loops from downstream to upstream activities and vice versa, enabling processes such as change management and issue and defect tracking.
Leading manufacturers integrate planning and simulation tools for up-front validation of manufacturing processes to develop ‘right-the-first-time’ manufacturing plans, reduce the risk of errors in manufacturing and improve quality. Smart manufacturing capabilities enable companies to analyze the impact of product mix on production to optimize overall production throughput-reducing non-value-added work and optimizing material flow and logistics. They can also better optimize equipment usage and more easily evaluate alternatives to determine, early on, how optimized throughput can be realized under typical mixed-model production scenarios.
To work more efficiently and be more competitive, heavy equipment manufacturers require configured, intuitive, and up-to-date information available on the shop floor via online electronic work instructions. These work instructions contain assembly sequences, visual data, and animations that can be automatically retrieved for any given production order based on a plant-specific process definition. Having direct access from the production work context, with information about assembly station layouts, parts, and tools to be used, helps production personnel report non-conformance issues on the shop floor―another example of effective CLM.
Siemens’ Strategy for Smart Manufacturing
Siemens Digital Industries Software (Siemens) has recognized the industry’s need for a smart manufacturing approach to help their heavy equipment industry customers manage their increasing product and process complexity, as discussed above. Fundamental to their strategy is that companies need to be better able to deal not only with product complexity (e.g., CTO with increasing variations) but also manufacturing environment complexity (global sourcing and production with different processes at each plant) and the ability to deliver service both on-site and remotely.
The digital thread enabled Smart Manufacturing for Heavy Equipment solution helps customers improve communication and collaboration throughout their enterprise, as well as with suppliers, to discover manufacturability issues and opportunities earlier, to continuously reduce miscommunication, mistakes, and overhead costs on the shop floor, to optimize process KPIs, and to build know-how about their global manufacturing ecosystem. This can help them achieve zero-defect manufacturing everywhere while driving sustainability.
Figure 1 illustrates Siemens’ approach to smart manufacturing for heavy equipment.
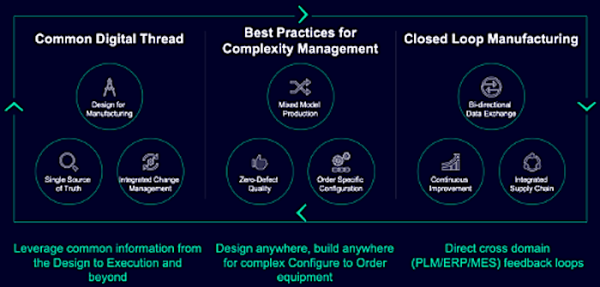
The Siemens Xcelerator portfolio is a comprehensive, integrated suite of software, services, and application development platform that provides the foundation for smart manufacturing. It helps businesses leverage complexity as a competitive advantage and transform themselves into digital enterprises faster. Characteristics of this portfolio particularly pertinent to the manufacturing of CTO products are:
- Comprehensive digital twin comprising a digital fabric of information from product design, manufacturing, and in-field utilization data, enabling cross-domain engineering, virtual validation, and continuous product and process improvement through a closed-loop feedback system.
- Personalized, adaptable solutions adapted to each heavy equipment maker’s digital roadmap and uniqueness.
- Open, modern, ecosystem that can adapt as technologies and business strategies evolve.
Figure 2 shows what is needed to bridge the gap between design and execution.
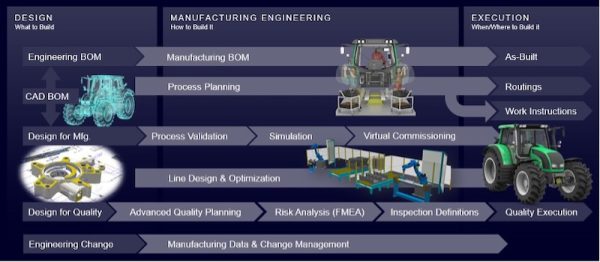
To enable efficient smart manufacturing that closes the digital gap from product design to production execution and makes digitalization a reality in the heavy equipment industry, Siemens Xcelerator includes the following key capabilities:
- Product Configuration provides the ability to configure a Manufacturing Bill of Materials (MBOM) into a specific customer order in a CTO business.
- Manufacturing Planning for the design and implementation of the Manufacturing Bill of Process (BOP).
- Process Validation enables virtual validation of product assembly and related process plans to eliminate potential shop floor issues.
- Advanced Planning & Scheduling analyzes achievable production schedules, considering a range of constraints and business rules, allowing the planner to generate and evaluate multiple potential scenarios.
- Production Execution & Optimization integration with manufacturing execution systems enabling the creation of a comprehensive digital twin used to continuously optimize production.
- Data & Change Management to handle the large amounts of data and changes that occur throughout the product, production, and service lifecycles.
In addition, using IIoT platforms like Siemens Insights Hub, production machines and systems can provide direct, immediate feedback from the shop floor to engineering and process planning users and systems, promoting continuous product improvement and eliminating knowledge gaps between engineering and execution.
Summary
Heavy equipment manufacturers are confronted with increasing complexity―both in product variations and global production operations. They need effective smart manufacturing capabilities that integrate their product development, production, and services processes and environments.
Siemens Xcelerator portfolio solution is designed to enable heavy equipment manufacturing enterprises to efficiently produce highly complex CTO product variations. It helps companies establish digital thread enabled CLM environments that can more quickly and efficiently manage change between product engineering and manufacturing so that product and production changes are kept in sync, and issues are identified and resolved earlier in the lifecycle when costs and risks are lower. This enables them to plan, produce, and service products as required to meet global, local, and specific customer requirements.
CIMdata believes that Siemens’ approach and solutions for smart manufacturing provide a very effective platform that can help heavy equipment manufacturers build better, more effective, and more profitable businesses; improve their overall product engineering-to-production efficiency; and improve their market competitiveness. With Siemens Xcelerator solutions for manufacturing planning and validation tied together through a digital thread, companies can create a smart, collaborative manufacturing environment that closes the loop between design and production and drives high-quality CTO products and services. Manufacturing enterprises facing today’s complexity challenges should include Siemens in their evaluation of solutions for smart, collaborative, closed-loop manufacturing.
[1] Research for this commentary was partially supported by Siemens Digital Industries Software.