Key Takeaways
- Model-Based Product Development (MBPD) involves interconnected design, simulation, manufacturing, optimization, and other technologies, operating on a common, native CAD model integrated into the engineering design environment.
- Manufacturers are striving to achieve the full MBE vision, which PTC believes is driving a stronger than ever commitment to Model-Based Product Development.
- To meet evolving customer needs toward MBPD, PTC has acquired or built advanced functional capabilities like real-time simulation, and generative design and integrated them into the native CAD environment, which is driving accelerated adoption of the capabilities.
- As companies advance digital strategies, MBPD will be crucial to achieving MBE’s full value.
Today, product manufacturing companies face increasing challenges, including time to market, supply chain disruptions, and the cost of poor quality. Their biggest test deals with their ability to consistently deliver product innovation to keep pace with the overall market's rapid advances in innovation. To help, there has been a strategic move toward model-based definition (MBD), the semantic definition of the 3D product model, and leveraging it in downstream applications for manufacturing and support, identified as model-based enterprise (MBE).[1]
PTC is focused on providing a design environment that encompasses the MBD and MBE strategy but goes further in solving the siloed processes of engineering and product design upstream that they call Model-Based Product Development (MBPD). MBPD is defined as a unified platform and a common CAD model across the core set of tools and functional capabilities required throughout the full engineering lifecycle.
PTC asserts that "context switching" inefficiencies occur whenever a user exits the CAD design environment to use an alternate solution for some aspect of the development process, such as surfacing, NC Toolpath development, mold tooling, and/or full mold base development. This often occurs for historical reasons, where in the past, the primary CAD solution did not have the functional capabilities or was weak relative to alternative solutions. The choice then became engrained in the development process even if the primary CAD solution gained the needed capabilities and surpassed the alternatives.
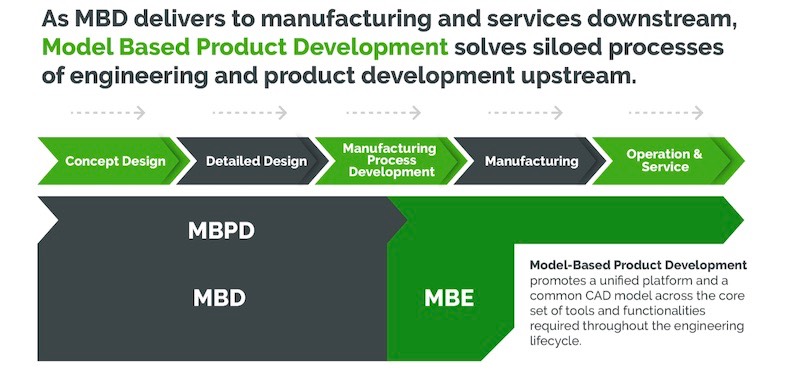
Figure 1―Model-Based Product Development
(Courtesy of PTC)
Creo's Breadth and Depth
Today, PTC's Creo supports a wealth of mature capabilities to match the best found in external solutions. While originally establishing itself as a leader in parametric modeling, PTC has enhanced Creo with direct modeling with Creo Flexible Modeling expertise and both parametric and freeform surface design.
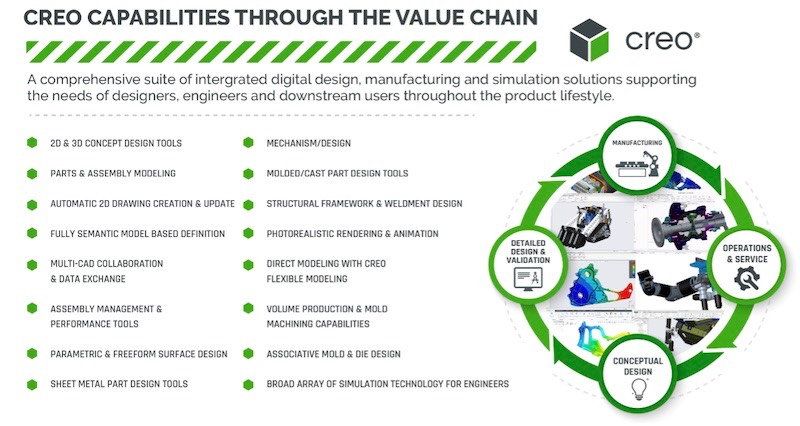
Figure 2―Creo Capabilities
(Courtesy of PTC)
Users have the choice of an extensive range of focused design functions spanning sheet metal design, mechanisms, molded and cast part design, as well as structural framework and weldments. The need to exit Creo to leverage an alternative capability has been minimized.
Emerging Technologies
The industry is experiencing an upheaval of design and manufacturing processes that is helping drive product innovation. Advances in artificial intelligence (AI) and machine learning are allowing engineers to explore numerous design requirements by varying loads and constraints, materials, and manufacturing processes.
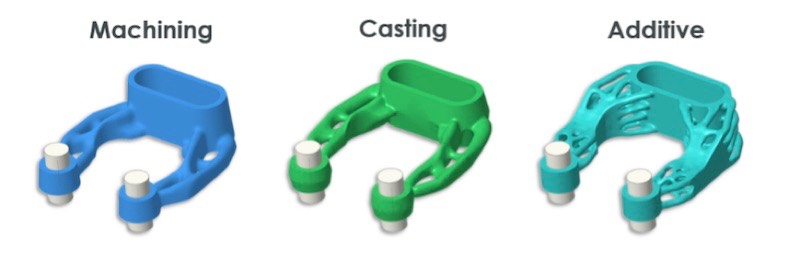
Figure 3―Creo Manufacturing Definition Supported by Generative Design
(Courtesy of PTC)
Generative design driven by AI can refine the product model with each iteration toward a design goal. The approach can offer differentiated products, reduce time to market, and optimize material usage driving down costs.
Simulation-driven design provides engineers with real-time design guidance. PTC delivers integrated Ansys real-time simulation that helps reduce labor and prototype costs, improves product quality, and drives innovation.
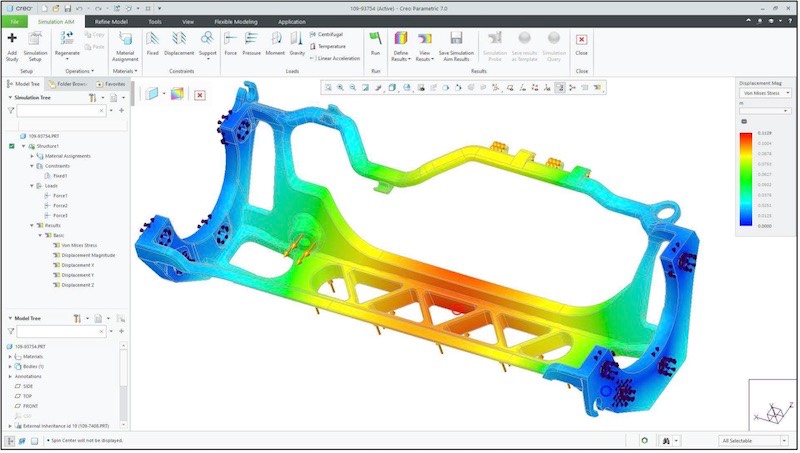
Figure 4―Real-Time Ansys Simulation Integrated in Creo
(Courtesy of PTC)
Design for additive manufacturing can deliver product solutions unheard of using only subtractive manufacturing processes. Designers can create, manage, and optimize designs for printability. Creo provides flexibility in designing lattices using parametrically and numerically controlled patterns. These techniques help reduce errors and waste. They lower production time and help drive innovation.
Conclusion
PTC's concept of Model-Based Product Development seeks to deliver the goal of model-based design throughout the full product lifecycle. By raising the bar in achieving a full MBPD platform for their users, PTC positions itself as a thought leader in the industry and delivers advanced capabilities to enable user innovation. CIMdata recognizes the PTC model-based strategy as a worthy solution for consideration.
[1] Research for this commentary was partially supported by PTC.