Key Takeaways
- Stored electric energy sources are expanding rapidly using both chemical and solid-state technologies.
- Companies need new, robust digital solutions that enable the design and manufacturing of innovative battery systems for existing products.
- New battery technologies are emerging and evolving faster thanks to inexpensive, connected sensing, and machine-learning digital twins that improve understanding by exposing design weaknesses with expansive “destructive” simulations, i.e., improving product robustness, especially safety.
- The stronger collaboration between the Automation and Software business units of Siemens Digital Industries is designed to cover the entire value chain of battery manufacturers. Siemens is supporting newcomers and incumbents as they accelerate battery cell and pack design, incorporate intelligent technologies and automation into battery cell and pack production, and streamline automation machine engineering through standardization and disruptive technologies including AI, IoT, and Edge.
Introduction
There is a rapidly increasing demand for higher energy density, longer lasting batteries. Batteries are being used in many new ways to provide energy storage for propulsion and systems operation, from cell phones to vehicles and aircraft to homes and buildings. There is a growing demand for electrically powered systems needing new, more capable batteries. Sustainability and greenhouse emissions awareness are driving demand for newer, more reliable batteries. Battery engineering challenges include energy density, faster charging, reliability, and learning for usage experience. This is coupled with the challenges of battery mass production―scaling up volumes while limiting scrap rate, meeting quality targets, maximizing throughput, and creating improved packaging. Battery pack and cell energy storage options are increasing as more investment is being focused on improving energy density―the amount of energy stored in a specific volume. The higher the energy density, the longer a system can operate between charging cycles and deliver better customer experiences, i.e., longer vehicle ranges. Charging and discharging dynamics affect battery durability and safety, which require the use of multi-disciplinary simulation and data collection to accelerate learnings and improve quality levels. Recent mass production battery systems advances are dramatically improving the amount of stored energy available in many different use cases.
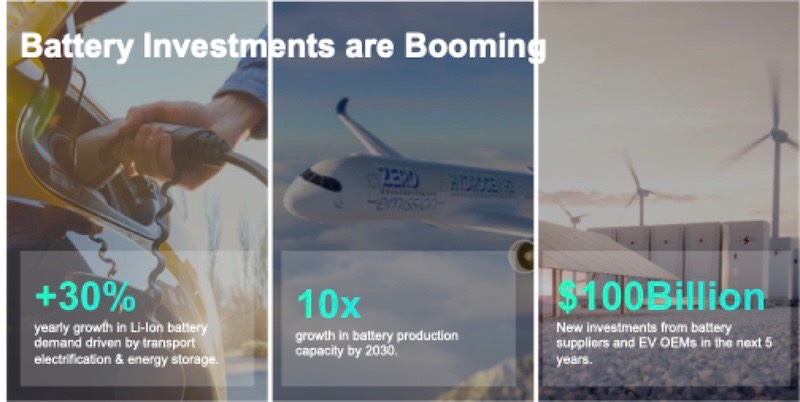
Figure 1―Batteries are Broadly in Demand: for Vehicles, Aircraft, Energy Storage
(Courtesy of Siemens)
Major trends disrupting the manufacturing industries, like product electrification and reducing carbon footprint, have driven the need for increased investments in digital technologies used to modernize production facilities and processes among battery companies of all sizes. Challenges with growing battery systems complexity, battery raw material availability, operational flexibility and speed, and supply chain create additional headwinds in highly competitive battery production global markets. New materials and construction will be needed to help lower system costs.[1]
Sustainability goals concerning how and where batteries are manufactured and used are quickly becoming policy and regulated. Battery recycling will help address raw material availability. Some governments are now requiring material and battery manufacturing be done within their countries, or at least by most favored trading partners. Material traceability, recycling, improvement in designs and circularity, and energy efficient factories are among the key challenges to overcome.
To deliver significantly higher energy density than today’s Li-ion battery technologies, new chemistries and material development is needed. Fire hazard and thermal management during power consumption and charging require new power management electronics and controls software. The speed of recharging needs to be balanced with durability and safety. The battery pack layout must be flexible given that individual cells are small compared to the number of cells packed together to achieve duration and range objectives.
In the automotive industry, post-production upgrades are improving battery life by adjusting the rate of charge and energy consumption for driving and passenger comfort. Embedded software systems and environment sensors are improving measurements taken during operation and bring insights to battery designers and engineers previously only obtainable via prototype and validation testing. Merging findings from customer usage with validation results as battery mass production proceeds provide product usage insights which can lead to upgrades in battery design and manufacture. The inherent increasing complexity of battery designs requires performance investigations on thousands of architecture variants to identify which one will meet all―sometimes conflicting―performance requirements. All of these aspects make it difficult to stabilize a production process when hundreds of parameters have to be taken into account.
Fast-paced design development and optimization of efficient, scalable mass production of batteries are key to success for many different products. While the electrical and mechanical aspects of such designs are being proven out, digital manufacturing needs to be applied to enable a streamlined launch process. Battery designers and engineers need to apply Design for Manufacturing (DFM) technology and processes to identify any assembly problems early and enable quick resolution of those problems. Battery units can be packaged in many different product configurations which can improve product performance, inherently leading to a more stable operation. For example, the center of gravity can be optimized, lower in ground transportation vehicles or ideally placed for stable aircraft operations.
The Important Role of Digital Thread and Digital Twin
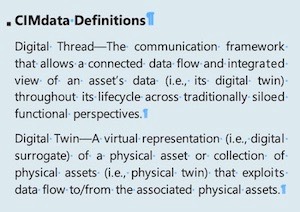
For many CIMdata clients a key goal is integrating product development with manufacturing using digital data. Digital manufacturing is built on a digital thread of related product definition and production process information. An effective digital manufacturing thread coupled with a production digital twin drive the digital manufacturing strategy.
Such a digital thread enables a digital manufacturing model, which allows engineers to generate, simulate, analyze, and predict production performance before investing in physical parts and initiating production. The thread connects data leveraging PLM, industrial internet of things (IIOT), and factory automation technologies, including 3D design, CNC programming, simulation of models, manufacturing processes, and manufacturing facilities design and operation.
Using digital twins of the production facility and processes enables accurate simulation and prediction of the physical twin’s behavior (and that behavior can be used to update and verify the models and processes). Data captured from the physical twin can be replayed within the digital twin to predict problems and to develop solutions that are then tested on the digital twin, shortening time-to-value and reducing the risk of harming or delaying the operation of physical assets and products. Models of battery manufacturing facilities and processes coupled with the ability to download CNC programs directly to the physical machines can dramatically shorten the time to commissioning and production. Operational Digital Twins will accelerate applied learning of actual battery use and shorten the discovery and resolution processes needed as new battery technologies are introduced to the market and mass production accelerates.
Siemens’ Solutions for Battery Advances
Siemens has decided to consolidate the Battery Industry Group and have Software and Automation join forces to deliver even more value to customers. This group is focused on the application of Siemens software, factory automation, and management solutions to the fast-growing energy storage in batteries market. Digitalization and automation are game changers in the development and production of next gen batteries. The massive amount of data generated needs to be collected, understood, and used intelligently―for example, to simulate and design new battery cells, optimize new production plants before they’re built and, above all, utilize valuable raw materials perfectly and with no waste. And bridging the gap between design and production and between the real and digital world through data continuity is what will help make a difference. This is the mission of this new battery group. It will leverage the Siemens Xcelerator portfolio of technology and solutions to provide a simple, flexible, and open digital business platform that helps the battery industry to innovate faster and ultimately become digital enterprises. Siemens also provides the digital manufacturing planning and operations solutions to enable the design, commissioning, and efficient, scalable, adaptable operation of new battery manufacturing factories. Siemens’ digital thread solutions broadly address the complete battery value chain, from materials to recycling, including battery design and engineering, to all manufacturing steps.
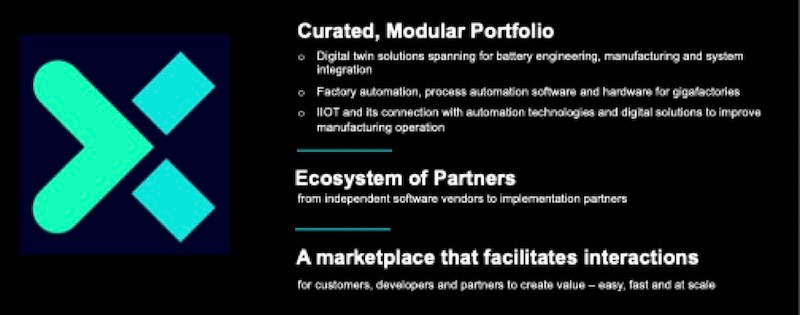
Figure 2―Siemens DI for Battery is Broad
(Courtesy of Siemens)
Siemens has a rich history of providing innovative solutions and key discipline integrations for electrical and mechanical engineering, as well as manufacturing planning and modernizing factories with machine automation, IIoT data sensing and collection, including relationships with machine builders. The use of executable digital twins, using the data and traceability solution capabilities, can help product developers meet the correct set of requirements, even as those requirements change during development.
Several CIMdata articles summarize the expansion of MBSE driven, multi-discipline capabilities that Siemens has built. Siemens’ solutions are already enabling advances in electric vehicle engineering, systems and software engineering, executable digital twins, manufacturing planning, and operations, all contributing to accelerating every aspect of product development, production and use. They are now focusing those capabilities on battery engineering and mass production challenges.
Siemens’ Xcelerator Portfolio Speeds Battery Mass Production
Siemens’ digital manufacturing solutions are part of Siemens’ Xcelerator portfolio―a comprehensive, integrated portfolio of software, services, and an application development platform. It is designed to help companies transform themselves into efficient digital enterprises by providing solutions that can be incrementally acquired, personalized, and adapted to fit their specific business needs.
Importantly, Siemens Xcelerator is delivered as an integrated, modular portfolio of compatible solutions so that a battery company of any size doesn’t need to commit significant financial resources up front―they can evolve and grow at their own pace. Using the appropriate Xcelerator components, battery innovators can build the digital manufacturing environments needed to achieve and maintain their market competitiveness.
As the Siemens Xcelerator platform grows over time, most of its solutions are already available as a service. This will provide battery companies access to the latest available technology when and where they need it, with operational expenses based on consumption, maximizing flexibility.
Siemens Xcelerator portfolio and its battery solutions support initiatives such as Industry 4.0, smart manufacturing, the IoT and IIoT, edge computing, the move to smart, connected products, and digital transformation, among others, were introduced in mature products to improve customer satisfaction and reliability. These same technologies and solutions will enable companies to accelerate the battery design and production advances required to support new, higher performance batteries. Battery designers and producers implementing digital technology and practices will lead the race to new energy storage systems.
Helping battery companies, many of which are start-ups, recycle used or discarded batteries will also become a major new industry segment, just like it was in the past for steel recycling. Companies will need to apply solutions like those from Siemens, not just for engineering, but inclusive of manufacturing planning, mass production execution, and tracking deployed products.
Conclusion
The consolidation of the Siemens’ Battery Industry Group announcement comes as no surprise to CIMdata. After decades of accelerating automotive, industrial, and aircraft design, engineering, and manufacturing, it is what we come to expect from Siemens. CIMdata believes that proven PLM solutions from Siemens focused on evolving battery technologies can provide quantifiable benefits for companies that need to improve their battery design, agile manufacturing, and use including recycling. Data from engineering to production, test, and quality are available in a single, logical repository, giving better collaboration for battery engineers, manufacturing engineers, and CNC programmers so they can simulate and apply digital twin technology to speed up and optimize battery manufacturing.
Market and material pressures are forcing battery companies to remain agile in the way they create, manage, and leverage all their assets―human, physical, and financial. The digital thread and digital twin are capabilities from Siemens that will enable companies to effectively connect existing applications, data repositories, and development and manufacturing processes. Using a digital thread-driven digital manufacturing environment can enable battery companies to operate more efficiently and more quickly to deliver better products with a higher value add to their customers. Early adopters of Siemens portfolio of battery engineering and manufacturing solutions are enthusiastic, see Figure 3.
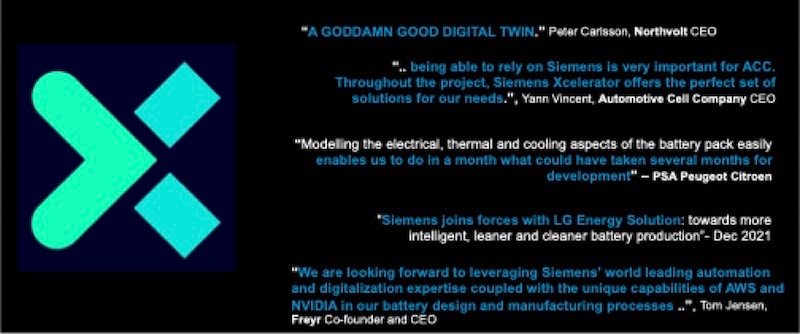
Figure 3―Siemens’ Customer Testimonials―A Critical Partner in the Battery Industry
(Courtesy of Siemens)
Siemens Xcelerator portfolio enables the digital environment that spans the complete battery design and production processes, allowing battery manufacturers, experienced and new, of all sizes to create and execute their business-specific digital manufacturing initiatives more effectively. It is designed to be integrated and adopted in affordable increments. Companies only invest in what they need, when they need it, and then can grow their digital manufacturing environment in small, affordable increments as the battery business evolves. Battery mass production while applying new materials technologies into reliable electrical energy storage is a key to lowering greenhouse gas emissions. CIMdata recommends that battery engineering and manufacturing companies who are implementing new battery design and production processes and facilities include Siemens’ technology and solutions in their evaluation and selection initiatives.
[1] Research for this commentary was partially supported by Siemens Digital Industries Software.