Key takeaways
- Advances in high fidelity system simulation software and computing hardware have improved useability and performance, enabling engineers to bring simulation earlier into product development, especially decisions based on complicated, coupled physics, e.g., turbulent flows of gases and fluids affecting lifting forces, drag, thermodynamics, and structural loads.
- Simulation software primarily uses physics-based solutions to perform structural, thermal, and fluid-flow analyses and requires domain experts and historically expensive computers to get useful solutions. Often, empirical data drives matching algorithms to refine and validate models. This landscape is changing thanks to algorithmic refinements using mathematical formulations and ubiquitous computing.
- Ease of access, along with GPU and CPU acceleration within high performance computing, enable engineering simulations to be performed faster and earlier. These are computing technologies that may well expand to digital certification of products using simulation.
- High-order solver advances and methodologies being researched and implemented at Cadence are improving the accuracy of turbulence simulation results. Complicated equations like Navier-Stokes, once considered impracticable to solve, are now being solved with expanding levels of accuracy using these simulation advances.
Digital systems improve product robustness engineering by allowing designers to see more physical interactions across requirements and candidate solutions before a product is produced. Digital transformation leverages advanced multi-physics systems modeling and simulation software capabilities. Faster and cheaper computer hardware, known as high performance computing (HPC), allows simulations which took days to now be done in minutes. By using more high-fidelity simulations earlier, companies improve development processes to reduce physical prototype dependence. This shortens time to market and, in many cases, improves product quality. Competitive pressures are driving companies to broaden their use of simulation software. Yet there are still phenomena at the boundaries of product performance for which simulation does not yield accurate results. These situations require physical testing, especially for regulatory and safety certification.[1]
Cadence is expanding its System Design and Analysis portfolio to address state-of-the-art computational fluid dynamics (CFD). This transformation results in the ability to make better decisions, leading to better products, improved product launches, more satisfied customers, and better business performance. Cross-disciplinary teams working collaboratively while using the same trustworthy CFD simulations will develop enhancements and/or investigations from different expert contexts, while keeping the complicated flow physics in mind. Historically, this has been one of the areas done serially, as confirmation, instead of continuously during robust product development.
Advanced simulations of complicated physics let a company explore factors like safety margins, compliance, and performance that influence when and how design decisions are made. A safety margin example is aircraft noise management, which is often a certification requirement to land at specific airports―the aero-acoustic performance for certain metropolitan areas drives aircraft sales. Another consideration is passenger audio comfort from audible and shaking turbulence and jet engine noise. The correct balance between these requirements is what drives success. The balance is achieved with a progression of decisions improved by understanding the flow fields around a product.
Simulation has advanced the understanding of structural dynamics, basic heat flow, and stable, primarily linear vibrations. Simulation of turbulent physics involves finer mesh resolution, containing many more nodes, and thus requiring a lot more computational cost. Choosing the solving process and applying new ways of numeric optimization enables understanding when a particular solving method is adequate for making a decision. But to fully replace a physical prototype evaluation with simulation, the most advanced numerical solving challenges must be addressed.
Simulation experts organize their planning for analyses by considering the following. It’s not surprising to see the division between incompressible and compressible flows. Figure 1 summarizes the options when considering how to simulate fluid flows.
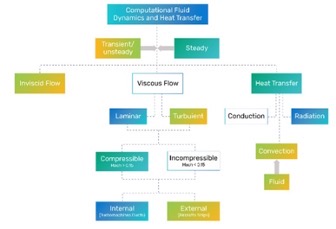
Figure 1―Potential CFD Fluid Flow Simulation Pathways
(Courtesy Cadence)
Compressibility can lead to a flow field disruption―a shock wave―where its physics exhibit abrupt changes. So, despite being all about fluids, CFD covers a wide range of fluid flows and types in which the physics differ greatly and where the governing equations become more complicated and computationally intensive. The Navier-Stokes equations comprehend all the physics, but when evaluated across meshes with hundreds of millions of nodes, they have been unreasonable to solve, until now.
Cadence’s Simulation Strategy to Push Digital Engineering Advances
Cadence is a leader in electronic design automation (EDA) where integrated circuit (IC) manufacturing processes drive what circuit geometries are allowed. Cadence’s tools have helped assure the continued realization of Moore’s Law. In fact, their EDA toolset is a major player in the advances of ICs inside HPC centers. Heat management in the chip, board, rack, and server rooms are critical factors as HPC capacities have grown. Now Cadence is investing in computationally intensive solvers for fluid dynamics of turbulent flows.
An inflection point is happening in CFD. Cadence’s acquisitions of Numeca, Pointwise, and Cascade Technologies are focused on improving algorithms to solve fundamental equations of complicated fluids behavior. By improving simulation at the difficult boundary conditions (e.g., turbulence driven noise and performance losses), Cadence is exploring and finding new algorithms and computing methodologies for solving the Navier-Stokes equations, the proper mathematical model of fluid dynamics.
For example, with visualization and faster equation solving for airframes, product performance predictions are more accurate because they better predict energy losses, in this case aerodynamic drag, which is directly related to airflow turbulence around a wing and fuselage. These predictions affect aircraft range and fuel storage needs. Another example is human centric: better understanding vibrations and noises which annoy the crew and passengers. Using simulations of the flow field and how noise and vibrations propagate, engineers can consider design alternatives.
Figure 2 summarizes Cadence’s capabilities, all of which contribute to shortening time to key product decisions. By using the appropriate accuracy for each decision being made, Cadence is accelerating engineering workflows. Being able to see results in a day instead of weeks or months improves collaboration and understanding among engineering teams.
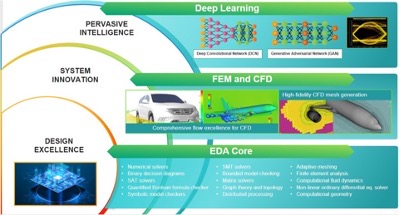
Figure 2―Cadence’s Solutions including CFD capabilities
(Courtesy Cadence)
Addressing the Edges of the Flight Envelope at Boeing
Leading companies, like Boeing Commercial Aircraft, are embracing this fundamental change in simulation capability brought about by advanced methods and ubiquitous HPC. Figure 3 shows an image resulting from accurate computation of the wing’s lift at high angles of attack, which is where the turbulent flow becomes separated from the wing leading to reduced lift. This is an example of perfecting the predictive abilities of simulation at the edges of the system’s performance, accounting for transient phenomena as well as the steady state. Results from this simulation matter when predicting or confirming that a future aircraft can meet performance, safety, and even noise regulations of suburban airports.
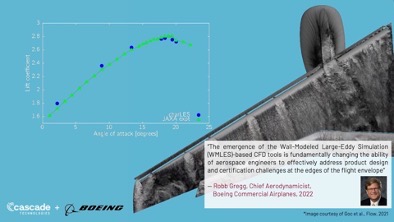
Figure 3―Boeing Experience with Cascade Technologies
(Courtesy Cadence)
Concluding Remarks
Ubiquitous high-performance computing continues to change engineering processes when performing more and more simulations. Numerically challenging equations can now be solved in time to make design tradeoffs, rather than relying only on best practices and/or physical evaluations. Applying HPC to complex physics contributes to improving the understanding of how turbulent flows affect performance (range, durability, noise, heat management) and will improve product designs.
The powerful CFD simulation capabilities from Cadence allow companies to better understand turbulent flows, both of liquids and gases, without waiting on expensive physical prototypes and wind tunnel testing. Of course, validation studies will be performed to improve the trust in the simulations. But once baselined, turbulent flow CFD simulations provide an investigation capability in hours instead of months. Cadence is no longer just a leading provider of electronic design automation tools where simulations are focused on electrical and thermodynamics aspects of the IC chips with their circuit board. Their advanced CFD simulation enables investigations, pioneered on aircraft, automobiles, and marine vessels, can now be extended to full electronic systems like servers, their racks, and even airflow in buildings hosting server farms.
Cadence acquisitions of Numeca, Pointwise, and Cascade Technologies is broadening its CFD capabilities and completes another piece of the simulation framework for model-based enterprises. Comprehensive, efficient CFD simulation for turbulent flows will be a competitive discriminator. CIMdata believes that companies using Cadence’s advanced CFD solutions will be able to support competitive continuous model-based engineering practices.
[1] Research for this commentary was partially supported by Cadence.