Key takeaways:
- PTC has developed an innovative product strategy built atop a product’s 3D model-based definition (MBD) core that facilitates the Digital Thread.
- The MBD Core enables a model-based enterprise beyond product design, to include the wider scope of supply chain, production, and service.
- The semantic content of the MBD core facilitates the Digital Thread through downstream applications including emerging technologies.
Developers of computer-aided design (CAD) products are actively implementing 3D model-based definition concepts within their software solutions. They add the semantic (machine-readable) knowledge that a given geometric construct is a feature of a particular type, such as a countersunk hole, a boss, or a variable radius fillet. Along with the feature knowledge comes the identification of the parameters and their values that define both the design and manufacturing aspects of that specific feature. The data represents the product manufacturing information (PMI) that can be displayed (see Figure 1) for a viewer’s better understanding of the product design. CIMdata thinks PMI is meant for much more.[1]
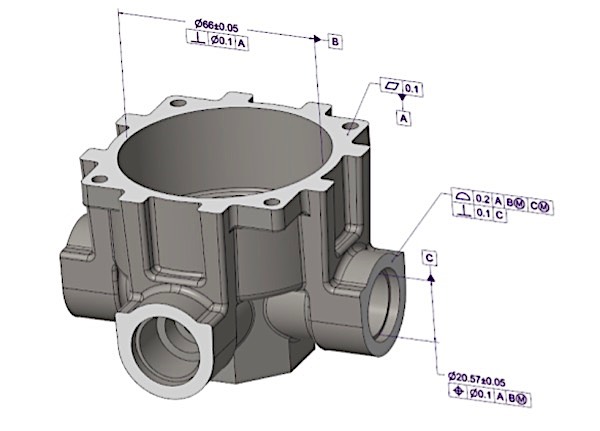
Figure 1―A Product Model with Associated PMI
(Courtesy of PTC)
The primary intended reason for PMI is to intelligently guide production personnel and equipment in the manufacturing of the product. Although semantic feature knowledge and associated PMI, generated during the product’s design phase, are compelling, their true impact results when that data can be used to invoke and drive downstream manufacturing equipment without human intervention. Today, MBD-powered solutions often fall short of this goal. CIMdata believes that CAD solutions that limit the use of PMI to simply display the data are missing the opportunity to provide intelligent impact for their users.
MBD Core
PTC has made their MBD implementation in Creo the semantic core of the product model where product manufacturing information (PMI) and other metadata is machine readable avoiding error-prone human interactions historically required to drive downstream applications like manufacturing and inspection. Creo’s PMI approach limits the need to display geometric dimensions and tolerances so that individuals must read the information and input it into downstream applications to drive them. With MBD at the core, the downstream applications can automatically identify product features and read the PMI to drive their own execution. As shown in Figure 2, PTC proposes that the semantic information can help bind together the product model and the surrounding CAD and other applications. CIMdata concurs.

Figure 2―Suite of Creo Capabilities Built Around the Product Model
(Courtesy of PTC)
All of Creo’s capabilities are built around the product model. Once created, each capability has access to the MBD and PMI features and data resident in the model. As they perform their function, those capabilities may add more information to the semantic model features that yet again other capabilities can access and leverage.
Model-Based Enterprise
Because MBD is at the core it forms the base from which users can extend to model-based enterprise across corporate disciplines such as manufacturing, quality, and in-service operations as well as into the supply chain. This knowledge extends across the full product enterprise referred to as the Model-Based Enterprise (MBE). For example, a component part might be tested for its manufactured tolerances during quality inspection, and its variance stored as semantic MBD information later used downstream to reset the necessary tolerance for drilling a hole in the component. So as the product model moves through its lifecycle, the semantic MBD information acts as packet of data being threaded through the design and manufacturing processes. It forms the base of the digital thread. CIMdata sees the power of this concept providing benefits to users for years to come.
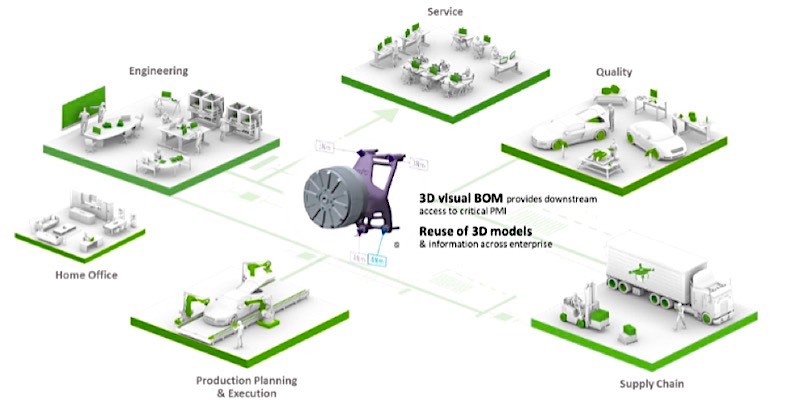
Figure 3―A Product’s Model-Based Enterprise
(Courtesy of PTC)
MBD Drives the Digital Thread
PTC has made the strategic decision to drive the product Digital Thread through downstream applications where they can machine-read MBD information and potentially add content to further improve downstream activities. MBD data weaves through the progressive stages of the product lifecycle providing bill-of-materials (BOMs) of as-designed, as-assembled, as-manufactured, and as-maintained.
Conclusion
PTC’s MBD story begins in Creo with the design-time creation of product features with semantic information and PMI. As the product moves through its varied product definition operations such as simulation, the MBD content helps drive those capabilities. Then as the product evolves through its lifecycle, MBD information continues to play a role in manufacturing and service. With MBD at the core, its impact in uniting all the many diverse disciplines of product development benefits the product developer by reducing design cycle time, providing faster time to implement changes, and reducing time from concept to delivery. CIMdata recognizes the power of PTC’s strategy of MBD at the core and expects to see many advantages for Creo users.
[1] Research for this commentary was partially supported by PTC.