Key takeaways:
- A closed-loop requirements view through all phases of the product lifecycle―from design to manufacturing and including customer use―is critical so that an Automaker can learn, adapt, and adjust continually to stay ahead of its competition.
- Only a fully integrated solution―one that is and remains integrated through a product’s lifecycle across all disciplines―can enable the process revolution essential to establish and sustain an automaker in a leadership position for tomorrow.
- Reducing early physical prototypes with simulation by relating requirements with test results enables repeatable, traceable correlation of virtual to actual performance.
- Concurrently examining how a requirement is implemented as the product design evolves is essential to all stakeholders across different disciplines.
- Siemens Digital Industries Software Systems Digitalization solutions are designed to keep teams integrated, improve decision-making across the lifecycle, and keep the relevant requirements visible all the time.
CIMdata’s definition of product lifecycle management (PLM) emphasizes the complete lifecycle of a product and all its related data, from requirements definition, through planning, development, supply chain participation, mass production, and actual performance in service including service, maintenance, and upgrades. Capturing, balancing, and viewing requirements in different contexts helps bridge disciplines allowing them to work more concurrently. Allowing more design options to be evaluated without delaying time to market. Having requirements managed in a central data repository managed with a PLM framework provides the stable backbone required for accelerated vehicle development.[1]
In a recent CIMdata white paper[2] covering Accelerated Product Development for automakers, we described the need for a broader view of collaborative engineering. In the white paper we identified two topics which are at the core of accelerating product development, namely auditable requirements traceability and continuous virtual verification and validation.
This commentary examines the needs of requirements management beyond product design and use. Consider the different ways requirements are viewed and the contexts which drive decision making. Understanding which requirements are mandatory and which are aspirational is important in commercial markets. Understanding how market changes are forcing requirements to change during development is another important risk which must be managed. Traceability is the capability to understand how a system and its components satisfy requirements. Being able to see the requirements relationships and influences easily makes them more comprehensive and auditable. What is needed is a solution which makes auditable and traceable requirements available all the time from any engineer―it is just the right information at the right time enabling the best decisions. Decisions improve when different contexts are evaluated. Figure 1 depicts the challenging scope of requirements for automakers competing with autonomous, electrified, and globalization themes.
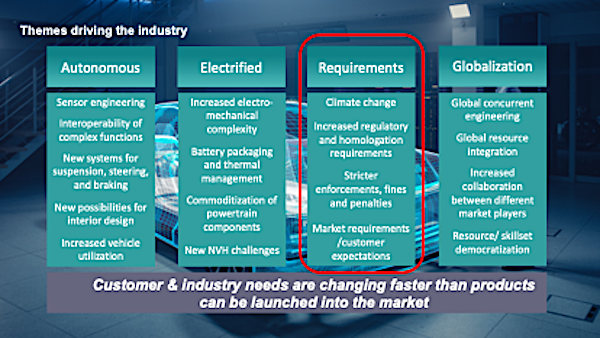
Figure 1―Competing Themes Driving Automakers
(Courtesy of Siemens)
For example, performance and emissions requirements often conflict. Even customer demands for towing capacity versus range conflict. With the advent of electric motor propelled vehicles, even the landscape of product solutions is changing quickly. Supply chain shortages from microchips to raw material are constraining requirements which must be addressed in concert with market drivers. Therefore, examining requirements traceability and making it turnkey, i.e., auditable, so all product development stakeholders use the same basis even though they approach the challenges from different contexts, is needed.
Teams work better collaboratively when they share the same trustworthy requirements data pool. They are addressing enhancements or investigations from different expert contexts. Contexts for decision making are improved when the requirements are managed and related to product usage patterns, ideally from real customer experiences. Doing these concurrently speeds time to market.
Reporting requirements satisfaction and compliance historically happens just before a product is put into the market. But this report is often just an audit to confirm compliance to regulations. Regulatory compliance is best assured when it is visible from the inception of a new product. Having the audit insights always visible from the product inception so that product decisions are made with compliance in mind is essential.
Managing requirements and their relationships, connected to performance results as they occur, provides all stakeholders higher confidence that a product will meet customer and government expectations.
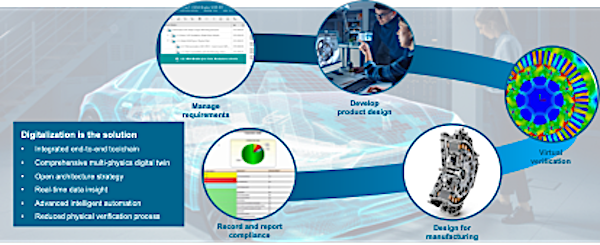
Figure 2―Digitalization Enables Requirements Management in Real Time as Auditable Traceability
(Courtesy of Siemens)
Figure 2 shows the focus for auditable requirements traceability. Note the summary points in the blue box: Digitalization is the solution which has:
- Integrated end-to-end toolchain, with an open architecture strategy
- Comprehensive multi-physics digital twin, using real-time data Insights
- Reduced physical verification testing with broader virtual testing
- Advanced intelligent automation, across disciplines
Digitalization not only makes engineering digital, but it will enable new types of businesses as processes and revenue models evolve. At the center of Digitalization is the need to manage requirements all the time.
Auditable Requirements Traceability Improves Cross-Discipline Collaboration
Siemens’ Accelerated Product Development Approach incorporates capabilities from their vast solution portfolio that enables requirements traceability to be done interactively. Doing this in real-time keeps requirements well connected and consistent. As shown in Figure 2, these requirements activities are best done continually rather than as book ends of the product development process as it has historically been done. These paradigms will enable process changes which the best automakers will take advantage of to lower time to market and development costs.
For example, Siemens’ Integrated Electrical and Electronic Solutions[3] (aka Capital and related E/E tools) are connected to NX. The two contexts of a particular signal in the door of an automobile, see Figure 3, are highlighted in both windows. Both views provide a specific discipline context but use the same requirements data backbone.
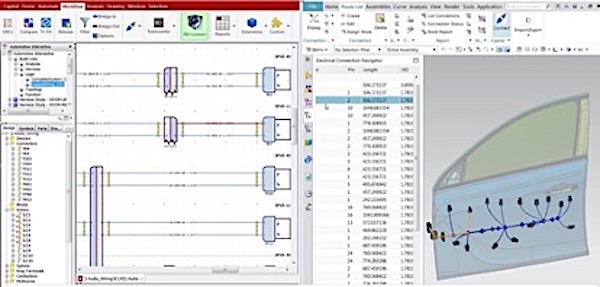
Figure 3―Orange Signal Viewed Simultaneously in Electrical Logic (Capital) and Mechanical Packaging (NX)
(Courtesy of Siemens)
As the electrical engineer establishes the context of the signal by selecting it, in real time the mechanical door engineer sees where that signal is routed. Their electrical/mechanical collaboration is sharing the same signal context from different points of view. There are other views of heating and vibration as CAE models are applied and again the design performance characteristics can be examined simultaneously across both domains, shortening problem resolution time, and eliminating extra repair loops. Characteristics are related, sometimes directly and other times indirectly, to specific requirements. Having requirements which are simultaneously satisfied from both contexts yields a better design and a more efficient change process. This will lead to improvements in multi-discipline change processes―they can happen in hours instead of weeks.
Scenario based testing comes from empirical data, even after the vehicle is manufactured. These testing scenarios can define new contexts, and the best empirical data establish the appropriate digital twins. Requirements related to measures, the empirical data, provides the basis for traceability to usage. With traceability to usage and traceability to design elements, even if they are from different disciplines, the requirements are easier to audit regardless of the contextual view. Digital threads and comprehensive digital twins provide the backbone for effective auditable requirements traceability. Regulatory reporting becomes automatic as the product is approved for mass production. Updates to the regulatory reporting, as product usage upgrades are released, also become automated.
Concluding Remarks
Requirements management done continuously is a competitive advantage, improving cross-discipline contextual collaboration. Furthermore, a comprehensive digital twin, always accurate to the latest empirical discoveries and associated to product requirements, is possible. This is achieved by examining the data and traceability solution capabilities, making sure product developers are always using the correct set of requirements–even as requirements evolve during development. Siemens’ multi-domain information backbone which includes all product requirements and constraints, has been designed to continuously connect engineers by providing an accurate digital twin of the vehicle design, its manufacturing, and its use.
CIMdata recommends that automakers consider Siemens’ portfolio of solutions to accelerate their product development. Electrical and mechanical engineers can work together simultaneously on a design. With computers and their associated electronics being pervasive, a comprehensive, integrated yet heterogeneous, multi-disciplinary product development environment connected to all stakeholders for all disciplines is possible. Siemens’ APD solution set broadens requirements management capabilities enabling auditable traceability. Siemens’ advances in Quality Management,[4] Systems Engineering,[5] Simulation with Executable Digital Twins,[6] Connected Engineering,[7] Systems of Systems Frameworks,[8] and future concepts in the works can provide a rich set of capabilities that product designers will use to develop the next generation of vehicles. This is what happens when a leading solution provider builds on their strengths.
Continuous Virtual Verification and Validation is the final commentary in the APD solution story, and it will be published later in the Summer of 2022.
[1] Research for this commentary was partially supported by Siemens Digital Industries Software.
[2] See: Accelerating Product Development―Faster Decisions while Reducing Physical Prototypes. 2 March 2022. https://www.cimdata.com/en/resources/complimentary-reports-research/white-papers.
[3] https://www.plm.automation.siemens.com/global/en/webinar/vehicle-electrification-integrated-ee-systems/104499
[4] https://www.cimdata.com/en/resources/complimentary-reports-research/commentaries/item/16341-a-broad-approach-to-quality-management-commentary
5] See: Driving the Change for the Future of Automotive Development. 24 November 2020. https://www.cimdata.com/en/resources/complimentary-reports-research/white-papers
[6] https://www.cimdata.com/en/resources/complimentary-reports-research/commentaries/item/16725-siemens-making-the-digital-twin-executable-predictively-aligning-its-real-world-counterpart-highlight
[7] https://www.cimdata.com/en/resources/complimentary-reports-research/commentaries/item/14887-connected-engineering-accelerates-innovation-commentary
[8] https://www.cimdata.com/en/resources/complimentary-reports-research/commentaries/item/17304-siemens-broadens-mbse-to-engineer-beyond-individual-autonomous-vehicles-commentary