Key takeaways:
- To bridge the gap between today’s advanced driver-assisted systems and tomorrow’s fully autonomous vehicles (AV), transportation management systems, from fleet coordination to traffic management, must be well connected.
- New sensors, automotive software including on-vehicle embedded and off-vehicle (cloud) software, and computing advances are the building blocks enabling advanced driver-assisted system (ADAS) features and eventually driverless autonomous vehicles. Connecting empirical data for model validation, will enhance collaboration between all stakeholders during AV product development and operations.
- Connectedness will keep AV products safer while improving the travel experience by reducing traffic congestion and driver workload.
- Connectedness allows new groups outside of historical vehicle engineering and manufacturing to assist in operations and product/service upgrades based on the latest usage patterns.
CIMdata’s definition of product lifecycle management (PLM) emphasizes the complete lifecycle of a product and all its related data, from requirements to actual performance, to planning and supply chain participation, then mass production, product service and upgrades, and finally decommissioning/recycling. Systems Engineering improves Autonomous Vehicle development and operations by considering a broader context—one that includes the operational environment of the vehicles.[1]
In a recent CIMdata eBook[2] covering AV development, we described the need for a broader view of collaborative engineering and operations where the AV may well rely on feedback from the city and other AVs’ sensors to provide safer, efficient route guidance, and robotic driving. In the eBook we summarized AV challenges as follows:
“There remains a gap in the journey from today’s Level 1, 2, and 3 ADAS capabilities to capabilities needed for a fully AV…With AV development, integrating the sensing, communications network, and traffic management beyond the vehicle will be required to bridge this gap. Complexity grows as connecting vehicles to different infrastructures expands. Connected transportation systems with AVs go beyond the boundary of an individual vehicle. Complexity is caused when connecting vehicles to different infrastructures—starting with service and moving quickly toward travel efficiency. A system’s engineering view of these different systems’ boundary diagrams shows that the vehicle is now a sub-system of a connected transportation ecosystem.”
Figure 1 shows the many systems of systems in AV product development contexts, from chip to system to vehicle to city, which is driving Siemens AV solutions development.
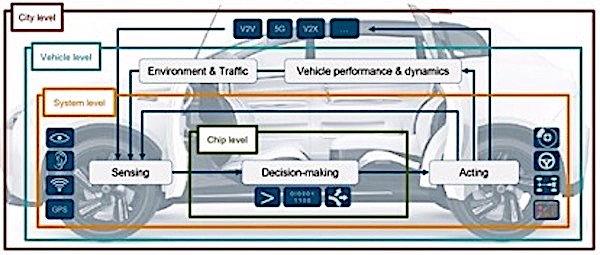
Figure 1—System of Systems AV Product Development
(Courtesy of Siemens)
Connectedness Improves Learning, Adaptation, and Collaboration
Connectedness is the collection of capabilities needed to keep models trusted, help teams collaborate faster, and provide frameworks to work across cities and automakers. At the core of this is communications. When combined with city level abstraction, see Figure 1, and architectural frameworks, an even broader ecosystem must be integrated with communications—all forms of connections. Organization-to-organization coordination and the possibilities for supporting continuous improvement of AVs during operations are easier with constantly connected communications. Improving safety by utilizing trusted, shared models that learn from expansive sensing of the vehicles’ operation is now possible. Building trust in the operational environment requires an application of systems of systems thinking, starting with systems engineering practices applied to not just the AV’s development, but also the environment in which the system operates, especially as that environment changes. Connecting everything from sensing to engineers to traffic managers and their systems is needed for autonomous vehicles. Incremental enhancements to ADAS vehicles with new connections will be the basis to bridge the ADAS/AV gap.[3]
AV development requires considering complex operational scenarios that are easier to discover when applying model-based systems engineering principles supported by architectural frameworks that are designed to ensure consistency. Customers, automakers, and cities will use Artificial Intelligence/Machine Learning (AI/ML) with powerful computing platforms both within the AV and provided as a service from the city. By leveraging real-world measurements to correlate virtual model-based scenarios using digital twins to help assess complex operational anomalies will make AV upgrades safer and more reliable and thus earn customer and societal trust. Learning and adaptation keeps models trustworthy. Doing this in near real-time keeps them well connected and aligned.
The vehicle is connected to the environment via networks, the engineers are connected to real-world experiences via sensors in the product. This is all enabled by electrical, electronic, and embedded software development solutions where communication test cycles are conducted virtually and physically. These are key capabilities for successful operational upgrades after the AV is manufactured. One can even imagine different AV feature sets based on the specific city in which they operate, and then adapting as the AV moves from one city to another. Different cities will likely be at different levels of sensor fusion and traffic management. AV developers need to support these variations as the vehicle moves from one city to the next. Staying connected to the product while it is used in different cities will become a discriminator for successful AV operations.
Enabling AV adaptation via in-field upgrades using Over-The-Air upgrading capabilities to refresh vehicle software requires coordinating upgrade releases with back-office computer services (e.g., traffic management, route planning, and tele-communications connections). This will make connectedness continuous—always there, learning, and then deciding if adaptation is needed.
One last point—teams work collaboratively in parallel when they share the same trustworthy models as they are addressing enhancements or investigations from different expert contexts. Contexts for decision making are connected when the data used for model correlations is based on the appropriate usage patterns, ideally from real customer experiences.
How Siemens is Demonstrating Connectedness
Siemens recognizes that all core business processes for all product disciplines must stay connected and collaborate not only to produce an AV, but also to provide the appropriate services and upgrades to it during its useful life. This means connecting diverse data silos by providing a capable and flexible work product and empirical data repositories. Siemens’ solution set for AV Development (AVD) leverages their existing capabilities.
Siemens’ integrated Model-Based Systems Engineering (MBSE) solutions, described in a CIMdata commentary on Systems of Systems Development,[4] have been designed to help their clients bridge gaps between engineering disciplines, which in turn improves development collaboration, and even spans different organizations. Siemens’ Software & Systems Engineering (SSE) Connected Engineering capabilities provides an integrated, heterogeneous MBSE environment managing reuse of everything.[5] AV development and operations needs to expand beyond product engineering to include stakeholders outside of the automaker. Siemens’ Integrated Electrical and Electronic Solutions[6] (aka Capital and related E/E tools) provide the solution set to develop communications systems needed to connect vehicles with cities and automakers. Figure 2 depicts Connected Stakeholders using Functional Digital Twins which yields Trustworthy Models.
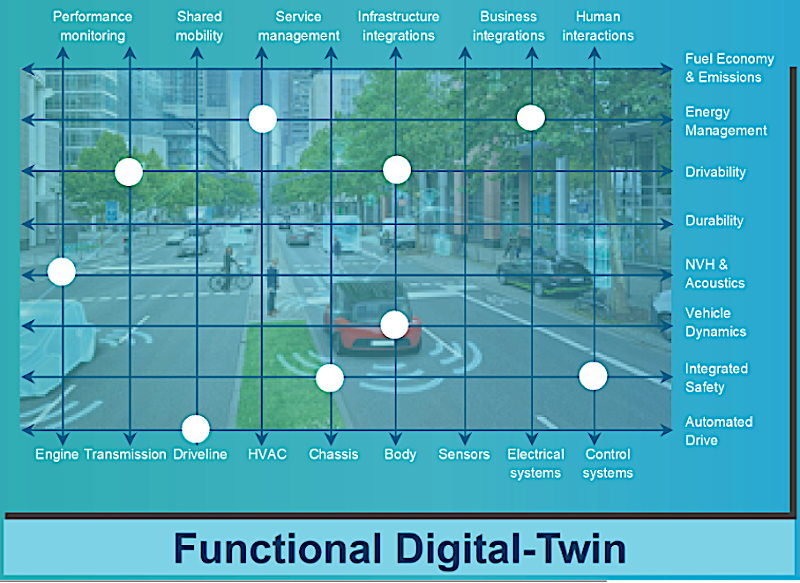
Figure 2—Connecting All Stakeholders with Trustworthy Models
(Courtesy of Siemens)
Scenario based testing requires empirical data, even after the vehicle is manufactured. Figure 3 illustrates how digital twins and threads lead to the authoritative source of truth with the broader AV product development contexts depicted in Figure 1. These contexts and the best empirical data establish the appropriate digital twins. AV development needs these broader domains to be connected, while providing their viewpoints (i.e., contexts) beyond any single vehicle. AV adaptation to its operational environment needs trustworthy digital twins of the systems they operate in (the city). Continuous upgrades and taking advantage of external sensing for traffic, obstacles, and even time of day will make for safer AVs. To enable continuous upgrades, the vehicles must be connected to each other, to the cities, and even to the knowledge repositories and engineers at the automaker and relevant service centers. Digital threads and twins provide the backbone for effective connectedness. Being connected well provides the accurate digital twins.
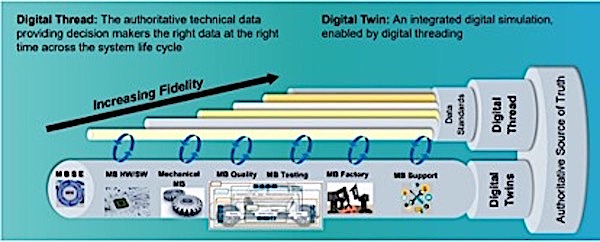
Figure 3—Digital Twinning and Threading Provides Truth
(Courtesy of Siemens)
As new AV empirical and associated scenarios are captured, models and their simulations will be improved, and quality risks and learnings can be explored. With AVs, this will include the city where it operates, which is outside the automaker’s span of control. The continuous training (aka adaptation) of models based on near real-time empirical data combined with fast, reliable communications provides more Connectedness.
Concluding Remarks
CIMdata forecasts that automakers connecting data with learning digital twins will realize significant benefits during AV development and operations—building trust with cities and passengers. Systems engineering is a competitive advantage, and when enabled correctly, product and process innovation are enhanced with contextual collaboration. Furthermore, a comprehensive digital twin, always accurate to the latest empirical discoveries, is needed. To support this, Siemens’ multi-domain information model has been designed to continuously connect engineers by providing an accurate digital twin of the vehicle design, its manufacturing, and its use. With the enablement of systems of systems development capabilities beyond a single automaker, Siemens provides a solution set ready for AV development and operations—supporting AV upgrades with their SSE, Capital, and now AVD solutions. By providing a framework for cities and automakers to connect, Siemens is addressing another capability needed to bridge the ADAS to AV gap.
CIMdata recommends that companies consider Siemens’ portfolio of solutions. With computers and their associated electronics being pervasive, a comprehensive, integrated yet heterogeneous, multi-disciplinary product development environment connected to all stakeholders (e.g., other vehicles and cities) is essential. Siemens’ AVD solution set broadens SE capabilities enabling a systems of systems framework well connected with all stakeholders, across many organizations, needed for AV development and operations. Siemens’ advances in Quality Management,[7] Systems Engineering,[8] Simulation with Executable Digital Twins,[9] Connected Engineering,[10] Systems of Systems Frameworks,[11] and future concepts in the works will provide a rich set of capabilities that product designers will use for the next generation of mobility—Autonomous Vehicles. The AVD focus from Siemens goes beyond a specific AV. Siemens is addressing gaps in AV development with engineering tools that can be used to explore operational conditions as they are experienced. This is what happens when a leading solution provider builds on their strengths.
Continuous Performance Engineering is the final commentary in the AVD solution story, and it will be published later in the Spring of 2022.
[1] Research for this commentary was partially supported by Siemens Digital Industries Software.
[2] See: Autonomous Vehicle Development Requires Closed Loop Solutions. 21 July 2021. https://www.cimdata.com/en/resources/complimentary-reports-research/white-papers.
[3] ibid.
[4] https://www.cimdata.com/en/resources/complimentary-reports-research/commentaries/item/17304-siemens-broadens-mbse-to-engineer-beyond-individual-autonomous-vehicles-commentary
[5] https://www.cimdata.com/en/resources/complimentary-reports-research/commentaries/item/14887-connected-engineering-accelerates-innovation-commentary
[6] https://www.plm.automation.siemens.com/global/en/webinar/vehicle-electrification-integrated-ee-systems/104499
[7] https://www.cimdata.com/en/resources/complimentary-reports-research/commentaries/item/16341-a-broad-approach-to-quality-management-commentary
[8] See: Driving the Change for the Future of Automotive Development. 24 November 2020. https://www.cimdata.com/en/resources/complimentary-reports-research/white-papers
[9] https://www.cimdata.com/en/resources/complimentary-reports-research/commentaries/item/16725-siemens-making-the-digital-twin-executable-predictively-aligning-its-real-world-counterpart-highlight
[10] https://www.cimdata.com/en/resources/complimentary-reports-research/commentaries/item/14887-connected-engineering-accelerates-innovation-commentary
[11] https://www.cimdata.com/en/resources/complimentary-reports-research/commentaries/item/17304-siemens-broadens-mbse-to-engineer-beyond-individual-autonomous-vehicles-commentary