Key takeaways:
- Digital transformation is a significant trend within manufacturing companies and requires new more automated ways of working that leverage digitalized information.
- While technology is available to transform to a model-based enterprise (MBE) strategy by leveraging implicit and explicit knowledge stored in 3D CAD models, most companies still use drawings and a variety of siloed repositories as their sources of truth thus breaking the digital thread.
- By employing a Design for X (DFx) strategy within a MBE, companies can evaluate, verify, and validate designs by leveraging the knowledge embedded in 3D CAD models. This not only accelerates the digital transformation process but also speeds up enterprise processes such as purchasing, manufacturing, assembly, and service, improving operations before products are produced.
- HCL DFMPro is a proven DFx solution that enables digital transformation and MBE by automating the validation of 3D CAD designs ensuring they meet necessary requirements.
Introduction
We live in an exciting time—digital transformation is happening everywhere you look, in our personal lives and professional lives, and especially in industrial environments. Understanding where to apply digital transformation in an enterprise is not always obvious. Changes in some areas can have a large effect and make material impacts on the bottom line. One of the difficult tasks for management is knowing which digital transformation opportunities to invest in to get the best return.[1]
Manufacturers in the automotive, aerospace & defense, industrial equipment, and high-tech electronics industries face exceptional competitive challenges and require both transformation and continuous improvement to survive. Transformation projects are designed to deliver big gains often resulting from significant investments in money and time. Continuous improvement focuses on making many small investments over time to stay competitive. Lean manufacturing is a well proven continuous improvement strategy implemented by companies. CIMdata sees the best returns in companies that take a strategic approach to transformation, based on a continuously improving roadmap with a strong architectural foundation.
Model-based enterprise (MBE) and Industry 4.0 are proven strategies that provide guidelines about how to achieve digital transformation and enable new platforms to support continuous improvement. While software is driving much innovation, most products still contain physical parts that perform functions that deliver value to the customer. Producing parts, assemblies, and complete products needs to be viewed holistically. Materials as well as design, production, and assembly processes continue to evolve providing opportunities for continuous improvement and transformation.
Successful Industry 4.0 and MBE approaches require 3D models and connected data so they can function properly. PLM solutions orchestrate the flow of data within processes ensuring configurations of data that describe products are properly created, managed, and consumed over the product lifecycle. Within the MBE approach information is organized into 3D models and related data and documents. 3D models can contain a plethora of important information that can be leveraged downstream as well as be used to optimize the product’s design and its production before it is released.
What is DFx?
Design For eXcellence expands the concept of design for manufacturability to cover a wide variety of design criteria such as service, assembly, safety, environment, and other constraints as shown in Figure 1. It is an approach to assess how well a design meets its requirements or constraints.
Figure 1—Common DFX Constraints
(Courtesy of HCL)
These requirements specify what design engineers need to include in the product to ensure the product will function properly. Historically this checking or validation occurred downstream long after the design engineers had moved on to their next project. Over the years DFx approaches have evolved from checklists and spreadsheets into software-based design assistants, checkers, and validators. These software tools have improved to include a wide variety of criteria to validate designs. In the most advanced situations, they are embedded within 3D CAD models ensuring that, during initial creation, designs meet product design standards, manufacturing process requirements, and downstream process recommendations, improving first-pass yield for products.
CAD Support for DFx
Historically, engineers and designers created drawings with dimensioned 2D views that were used to create products. Drawings also included tolerances, GD&T symbology, and notes to describe requirements needed for downstream functions such as purchasing, manufacturing, or service. Downstream work could not start until drafting was complete.
Modern 3D CAD solutions create and manage data that contains a tremendous amount of product knowledge in the 3D model itself. Geometry definition, part and product attributes, and product manufacturing information (PMI) including dimensions, notes, and GD&T symbology can be authored and stored within the CAD model linked to the appropriate features providing a single source of truth for this information. This data can be consumed and analyzed by DFx solutions and other downstream processes via APIs and web services. Furthermore, bidirectional integration between DFx and CAD streamlines the user interface and enables real-time DFx assessments allowing designers to quickly optimize their CAD designs, improve quality, and reduce engineering change volume.
DFx access to CAD data uses different methods including direct integration, and standards-based data exchanges. Standard formats such as STEP AP242, the ISO versions of JT, and 3DPDF enable DFx solutions to consume data without the need for the original 3D CAD application.
DFx-enabled Digital Transformation
Within a digital transformation roadmap, CIMdata believes DFx automation is a foundational enabler for process improvement. Any time human intervention is needed to complete a process, the digital thread is broken and the goal of digital transformation is compromised. DFx solutions validate product data (models and drawings) against industry and company standards via automated evaluation of rules rather than manual reviews. 2D and 3D data can be validated as it is created reducing and even eliminating manual checks. Figure 2 shows many areas where manual checking can be eliminated transforming processes and improving efficiency.
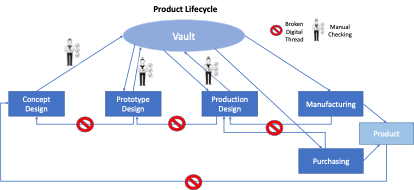
Figure 2—Common Areas where DFx Can Be Applied to Support Digital Transformation
Leveraging a DFx solution enables design engineers to check their design as it progresses getting feedback so when they release a design it will meet all company standards and guidelines. It can also be thought of as an inadvertent error prevention for design, dramatically changing the design process from its manual design-check-change process roots. This incremental approach to design ensures quality is designed in rather than inspected in via downstream reviews, shortening the design-to-production cycle time.
In addition to aiding design engineers in their day-to-day work, DFx enables significant process improvements when leveraging 3D CAD data. By validating designs with software, DFx can enable agile development methodologies within product design. The agile approach is well recognized in software development and is now being applied to the design of physical products. DFx tools can be used to perform automated checking in the same way that automated testing is used in software development.
The digitalization of the DFx validation process enabled by automated DFx checking also aids management. By capturing results of DFx checks and reporting on them over time, management is able to better understand how designs are progressing, speeding decision making. Review meetings can focus on critical issues rather than evaluating model and data quality.
DFx Results
DFx enabled design processes reduce time to market, reduce cost, and improve quality. It is easy to understand how ensuring tasks are completed up front reduces issues downstream minimizing scrap and wasted time. The automating verification tasks using DFx software can be done in minutes without interrupting design flow. Without software automation, checking must be done by an individual with the right skills when that person is available. In manual processes the queue time waiting for someone is often the longest time in a process.
There are many aspects of cost impacted by DFx. Assessing the manufacturability of parts for issues such as overhangs, radii values, sharp corners, too tight tolerances, and other common issues in the context of manufacturing process (e.g., injection molding, machining, forging, additive manufacturing, etc.) reduces part cost. For assemblies, product checks include fastener alignment, bolt and screw rationalization, and preferred hardware.
Using software to validate ensures that the checking process is repeatable and helpful to experienced design engineers, (we all make basic mistakes occasionally), but is extremely helpful for new hires and less experienced staff, not only do their designs get checked, feedback they receive speeds their education so they become experienced faster. Another benefit of the software is that it enables trade-off analysis. Parts can be assessed using different manufacturing processes such as casting vs. forging or how a design choice affects safety. HCL has seen the savings shown in Figure 3, when customers apply DFx as a part of their digital transformation.

Figure 3—DFx Savings Achieved at HCL Customers
(Courtesy of HCL)
HCL DFMPro
CIMdata has been following HCL for many years and published a commentary several years ago on DFMPro. We were impressed then and continue to be impressed by the new capabilities in the latest release. HCL continues to develop and enhance their product to keep its strong DFx support current. The most visible change is with the user interface. The latest update has a modern look and feel. Beyond the visuals they have added support for additional processes, additional coverage of out-of-the-box best practices, support for rules that leverage PMI and GD&T, and new customization capabilities. CIMdata is pleased to see HCL’s continued advancement of the breadth and depth of what can be assessed with their solution.
To better support digital transformation, HCL has improved the CAD/PLM integrations by supporting common solutions such as NX/Teamcenter from Siemens and CREO Parametric/Windchill from PTC. The integration with other platforms used to create enterprise digital threads is important as it enables deeper process integration, such as ensuring CAD data passes appropriate DFx checks before being routed to approvers or downstream operations via release processes. This method of ensuring improved first past yield of designs can dramatically reduce the number of engineering changes shortening timelines and improving quality.
DFMPro is now able to operate offline, leveraging server processing to enable the analysis of large volumes of data. Beyond the typical use case of reporting against large datasets, this is useful to identify legacy data issues such as parts which are not up to current standards and develop processes and action plans to address issues. It also provides foundational data to support artificial intelligence and machine learning solutions.
While DFMPro has always been configurable and customizable via its API, the new Visual Rule Modeler is a no-code approach to developing customizations. CIMdata is starting to see adoption of this proven approach in PLM solutions and is pleased to see HCL’s capabilities. This will allow customers to improve their digital threads with less effort and easier upgradability.
The last advancement to cover in this commentary is DFMPro’s new analytics support. While many companies have reporting strategies that leverage enterprise reporting tools such as Microsoft Business Intelligence (BI), applications need to provide access to data in context and in a form that reporting tools can consume. Often teams responsible for enterprise report development have large backlogs so applications with the ability for users or local administrators to create their own reports are very useful. DFMPro reports provides contextual reporting to design teams which cannot be provided by traditional or pure-play analytics tools due to HCL’s embedded knowledge of the DFx topic and data. HCL’s strategy is to move from using reports to describe what happened to becoming actionable by supporting prediction and prescription. With the PLM integration HCL can keep analytic results synchronized with the rest of the product definition captured in the digital thread ensuring traceability while making review and correction easier.
Conclusion
DFx is a proven solution to improve designs within enterprises. Modern implementations of DFx software such as HCL DFMPro can significantly improve enterprise processes by ensuring designs meet all appropriate criteria as they are produced. Fixing design issues early before they are physically instantiated is faster, easier, and cheaper.
At CIMdata we believe that to be successful digital transformation projects, need to focus on product lifecycle issues because the product is what provides the value customers pay for. HCL DFMPro is a tool that does a lot of heavy lifting to ensure designs meet their requirements across all the important domains: purchasing, manufacturing, service, and environmental. The ability to integrate DFx processes within a company’s digital thread as an interactive design tool and data quality validation solution is powerful so companies that want to improve the performance of their company’s digital thread should consider adding DFMPro from HCL to their process.