Helps achieve sustainable practices right and meet “Mission Zero” goals
Key takeaways:
- Automotive market demands have shifted and are focused on being more sustainable or “green,” while the classic competitive pressures of cost, time to market, and quality continue to increase.
- Electronic and software content continues to grow within automotive products as a cost-effective way to address market demands, but they add significant complexity to product development and production processes.
- Battery- and fuel cell-based propulsion systems required to meet zero emission goals require many new technologies to be leveraged and produced at scale.
- ESI’s virtual car prototypes help automotive OEMs and suppliers address the challenges they face within chassis lightweighting, electrification and batteries, safety, production process simulation, and customer experience simulation, with all of the different multi-domain simulation scenarios and data being managed end-to-end within one single core model.
Introduction
The automotive industry is arguably the most competitive industry in the world. Its operational scale and its impact on humanity and the planet are enormous. Over the decades automotive market demands have transformed from basic transportation equipment to highly styled, feature rich, reliable, performant mobility platforms. Over the past decade as awareness of sustainability has come to the forefront and as we humans better understand our impact on the planet, we are fortunate that technology is rapidly evolving to help create products that address sustainability issues.[1]
Climate change, resource use, and toxic pollution are global issues in need of solutions. Consumer demand and government regulation are the main drivers for change and within the automotive market, improvements in energy consumption, safety, emissions, and reliability are the most important characteristics to be optimized. According to industry research, 60% of companies in the automotive industry have a clear “Mission Zero” sustainability strategy.[2] They are striving to reach the “Mission Zero” targets for mobility products: zero accidents, zero injuries, zero emissions, and zero unplanned stops while providing hours of charged, maintenance-free range. CIMdata has been observing the sustainability trend for many years and is pleased to see solution providers enhance their design, simulation, and data management software to better support green goals.
Systems-focused design and simulation solutions have grown in capability and performance in recent years to support the concept of virtual product development and validation. Using computer models and simulations to predict product performance without building physical prototypes is becoming mainstream in all industries and is a basic requirement for success in industries such as automotive and aerospace.
Automotive Challenges
There is a common phrase, often attributed to a Daimler Chrysler CEO, that 90% of innovation in the automotive industry will come from electronics and software. While this is likely true, electronics and software also contribute significantly to the classic domains of metalworking, materials, and system design. Software is used to design products, the manufacturing process, and in many cases control the manufacturing equipment from an individual manufacturing step up to managing complete factories. Additionally, with the advent of smart, connected products, leading edge vehicles have live diagnostics that “phone home,” and even download software updates over the air (OTA).
While electronics and software may provide breakthrough innovation in advanced features such as autonomy, they also provide significant incremental improvements in traditional design of the body-in-white, chassis, interior, and other systems. These systems are core to performing the basic transportation function of moving people and goods from one place to another. Within these systems optimizing performance, weight, assembly processes, and service are critical functions that receive a lot of continuous improvement.
Improving customer experience with new capabilities and automation often combine many different physics domains with software. Mechanical, hydraulic, electric, and electronic capabilities are used to develop and produce capabilities such as electric vehicles (EV), advanced transmissions, safety related systems, infotainment, and autonomy.
The most important trend in automotive is the transition to electric vehicles. Moving from petroleum-based powertrains to battery-driven propulsion systems in vehicles requires redesigning vehicle architectures and systems to meet myriad consumer, regulatory, and societal requirements and regulations. For example, battery development has been a multi-decade journey to improve battery energy density while ensuring safe operation at a reasonable cost. But ensuring that batteries can store enough energy is only one of the many challenges related to electrification.
Safety requirements and solutions developed over the years have led to advanced features we take for granted today, such as crush zones, side impact door beams, airbags, anti-lock brakes, and stability control. Managing the heat generated in batteries to prevent fires is a major effort today driven by electrification.
Autonomy or self-driving vehicles cannot be done without simulation. The number of tests needed to sufficiently test algorithms and automotive systems such as steering and braking cannot be done physically in real-time. The only way to fully validate a modern vehicle is to do it virtually with simulation.
Having an innovative product is great, but if it can’t be produced to meet cost, quality, and time to market targets, it will fail in the marketplace. Capital investment and the effort to build up production lines and facilities is enormous. Complex factories with intricate layouts and large machines are required to produce vehicles as well as their systems and components. Vehicle designs change regularly, often requiring significant changes to production systems and regular production also drives changes as many factories are flexible enough to build product variants and even different products. Physically rearranging factories and lines to validate production is not reasonable. Stopping production to rearrange or reprogram equipment and to run validation tests won’t fit in the timelines and budgets companies need to achieve to be competitive. Virtual prototyping of production is a critical capability that leading manufacturers are adopting to shorten the design to production transition.
To address these many challenges, automotive companies need a comprehensive and extensible solution that can support the breadth of simulations within the larger context of delivering a product that meets a wide variety of requirements.
ESI’s Value
ESI, founded in 1973, is a leading software provider of virtual test solutions for the automotive and other industrial markets. Over the years their product portfolio has grown to meet the simulation requirements of their industrial customers. As computing power and software capabilities have evolved, ESI has moved to an industry vertical strategy. It has created solutions designed to meet the challenges of modern automotive development and production by focusing on virtual prototyping.
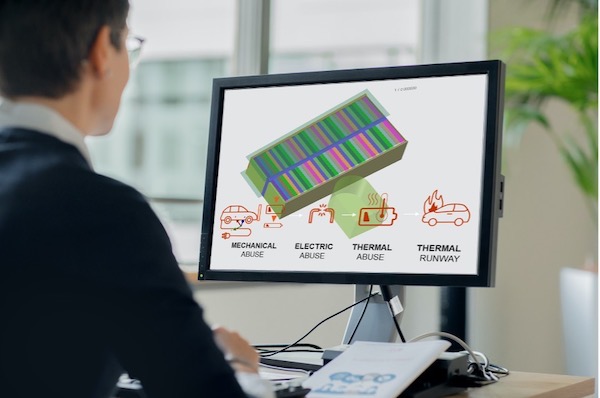
Figure 1—Using ESI Solutions to Simulate Battery-Specific Safety Norms Helps Protect Car Occupants and Pedestrians in Case of Failure
(Courtesy of Farasis)
Leveraging expertise in predictive physics-based modelling, ESI’s Virtual Car Prototypes enable their customers to study and optimize vehicle performance fully digitally. This allows designers to clearly visualize for instance, how the advent of high-performance batteries and lightweight structures affect the drivability and handling of the vehicle and its powertrain performance.
ESI has actively shaped product development processes since the first ever crash simulation conducted by ESI together with Volkswagen back in 1985 to predict VW Polo’s crash performance. Prior to this crash simulation, this critical compliance requirement was validated using expensive, time-consuming physical tests. The latest version of ESI’s Virtual Performance Solution[3] is used across industries to reduce the number of physical tests needed for development and validation. ESI’s automotive customers are using the technology to ensure EVs will be safe from the outset. The vehicle architecture changes required when moving from internal combustion engines to electric propulsion are significant. Weight distribution, types of systems and materials, and different hazards require many different load cases—to test all of them physically will slow product rollouts impacting business results. ESI’s approach to virtual prototyping is helping automakers accelerate their EV development and production by helping them shift to a “zero physical test and prototype” approach.
As experience with new advanced technologies grows, trust that they provide value (or not) also grows. CIMdata believes in the value of ESI’s virtual prototyping approach as it leverages their strong technology and is aligned with zero emission and sustainability requirements.
Conclusion
Competition in the automotive industry is fierce. Traditional business challenges continue to grow, and a recent addition is the challenge of sustainability. Mission Zero is an approach to sustainability adopted by many in the automotive industry and is focused on creating vehicles that are greener and safer yet still perform their intended functions with style and at low cost. To achieve Mission Zero goals, automotive companies are transforming to operate 100% virtual in an end-to-end fashion. This best-in-class approach uses a single logical source of truth for all data and product related information.
ESI’s Virtual Prototyping approach is helping major automotive OEM and suppliers meet the challenges they face in developing and producing new sustainable EVs. ESI has recently published an eBook that goes into more detail on virtual prototyping and will be having a dedicated automotive track at their annual ESI Live virtual conference on November 4, 2021. CIMdata encourages you to download the eBook[4] and attend the free conference[5] to learn how virtual prototyping improves R&D efficiency in the field of vehicle electrification. Automakers and suppliers that want to establish integrated and automated digital workflows to efficiently design, test, operate, and maintain future EVs while meeting the highest quality standards and lifetime performance, should consider partnering with ESI. Their proven solutions bring confidence early to all stakeholders involved in creating electrified vehicles at palpable ROI.
[1] Research for this commentary was partially supported by ESI.
[2] https://www.capgemini.com/de-de/wp-content/uploads/sites/5/2021/05/Experten-Interview-Die-Marke-neu-aufladen.pdf
[3] https://www.esi-group.com/products/virtual-performance-solution
[4] https://www.esi-group.com/industries/automotive/automotive-solutions#e-book
[5] https://www.esi-group.com/esi-live