Key takeaways:
- The cost of inventory is a significant and well-understood issue. While statistical models can help manage inventory, end customer satisfaction can be at substantial risk especially in the case of high value and low volume items.
- Technology evangelists often promote additive manufacturing machines that use metal or resin to create parts on demand to meet MRO requirements, but, while important, it only addresses a single dimension of the multi-dimensional inventory management for service parts.
- A robust, profitable solution addressing high-value, low volume inventory issues with digital technology must connect domains across the lifecycle to ensure speed, quality, and cost are repeatable and profitable.
- A practical, sustainable inventory solution is beyond any single enterprise or supply chain's ability and requires many cooperating participants.
- Wipro recognized that to be sustainable, the solution platform needed to focus on the industry level. Wipro has taken a proper integrator role and is acting as a liaison, platform integrator, and solution provider to implement digital inventory-as-a-service focused initially on the oil and gas and marine industries.
Introduction
Industrial domains such as marine, oil and gas, machinery and A&D are based on long-life capital equipment that generate revenue and value over years and even decades. The equipment is often complex and contain many unique purpose-built components and sub-systems. Downtime can be incredibly expensive, dangerous, and in some cases life threatening.[1]
To address the risk of downtime, the customers, OEMs, and service partners use several strategies to ensure maintenance, repair, and overhaul (MRO) is done effectively. Service contracts are common, and maintenance programs such as condition-based maintenance and predictive maintenance are becoming mainstream. In all cases access to spare parts is a critical element. The sad reality is that much of the inventory often goes obsolete and is scrapped before ever being used.
Additive manufacturing (AM) capabilities have reached production-level performance and promise to revolutionize spare parts management. While the 3D Printing/AM advocates had the correct vision and worked hard to increase their technology performance, they over-simplified the issues. Spare parts management is a complex system of systems problem and the additive manufacturing equipment is but one element. CIMdata is starting to see approaches that bring production worthy additive manufacturing into the product lifecycle where it can have significant impact on inventory management issues and ultimately reduce risk and downtime while improving satisfaction and profitability.
Physical Inventory Techniques Will Be Changing
Physical inventories of spare parts reduce the risk and impact of downtime, but at a cost. Given the pressures today on companies from globalization, competition, and regulatory changes that increase costs and drive prices down, cost savings are critical. While innovation is the long-term solution, cost reduction is the way to survive long enough to innovate. 100% of a cost reduction goes directly to the bottom line.
To shorten time to repair and reduce risk, companies keep spare parts in inventory, and OEMs or service providers have local and regional depots for spare parts. Spare parts management commonly uses statistical analysis of historical demand to forecast stock requirements. This works well for high volume items, but low volume items are more difficult to forecast. A cluster of failures can create demand that exceeds the number of spares available. “Out of stock” is a phrase that maintenance and service technicians don’t like to hear.
When a part is out of stock, and unavailable from a depot, it must be procured from a supply chain. If the part needs to be manufactured it can take weeks or even months to get a replacement. Delays caused by out of stock events add cost and reduce customer satisfaction.
Creating and managing spare parts drives the majority of physical inventory related costs. Supply chain issues include lead times, volumes, and safety stock. Low volume orders typically cost more, but perhaps even more critical is lead time. If a replacement part is out of stock it can take weeks or even months for one to be found or manufactured. High value asset owners can’t afford downtime, so they often buy their own replacement spare parts to minimize downtime. This is almost always done when the original machines go out of production and the few remaining parts needed get special ordered.
Ultimately much of this inventory ends up unused and adds significantly to overhead costs. For example, commonly the initial spares make up some 2 to 3% of the total purchasing costs of petrochemical and oil producing plants.[2] Within aerospace, inventory cost is estimated to be 25% per year, so for every US$100,000 of spare parts, the annual costs to hold them in inventory are US$25000.[3]
Additive manufacturing allows low volume or even single parts to be made on demand, which can be faster and less expensive than finding and shipping a replacement part from a warehouse. Older equipment operators will benefit from AM replacement parts delivered in a few days. Some predict that auto parts stores may in fact become replacement part manufactures for out of stock parts. But making the part reliably with alternative machines and equipment requires the inventory management technology to also track and reliably communicate properties beyond just dimensions and serial numbers.
As AM becomes proven, the digital record containing physical attributes of parts and manufacturing machine characteristics will need attention. To be sustainable, the solution platform needs to expand the collection of knowledge for reliably making replacement parts with AM. With adequate knowledge about the part, replacements can be made within a week or less. The need for inventories will decrease including their associated wastes.
Digital Inventory and Additive Technology
A modern lifecycle approach to developing products can support a different strategy for managing spare parts. Additive manufacturing is becoming mainstream and parts made using the various technologies are robust enough to meet difficult regulatory requirements such as those in medical devices and A&D. The production technologies have advanced to where product quality is predictable. Automakers and others are now making low volume parts with AM; gaining valuable production experience.[4]
The design and manufacturing technologies in use today are easily able to generate the data needed to produce products using additive techniques. For spare parts, especially those with complex shapes, additive is a boon. In subtractive processes such as machining, material removal can require extensive processing time, multiple manufacturing steps and setups. For molded, stamped, cast or forged parts, complex tooling is required. With additive a machine builds the part directly from a raw material, plastic, liquid resin, or metal powder, and the production rate is primarily dependent on the rate the material can be added.
With a modern lifecycle approach to product information, it is possible to maintain an end-to-end digital thread that ensures accurate parts can be produced on demand. Product designs are created as 3D models. Manufacturing software converts the 3D model geometry into a series of planar slices that get stacked together to control the build on the additive machine. Once the data for the part and manufacturing process is validated the digital files can be transferred to be built anywhere. The build sites can be distributed and only need to keep the machines and supplies of the appropriate raw materials on hand. These materials can be for processed into any shape required.
Digital Inventory-as-a-Service
While the ingredients for digital inventory-as-a-service are available, it’s a complex system of systems that is difficult to bootstrap into a sustainable solution. Elements of the solution include product design and manufacturing software, the digital product and process definition including quality requirements and verification, additive machine and material providers, and equipment operators. Getting all these system elements to work at the productivity, quality, and reliability levels needed for critical industries is not trivial.
CIMdata views this system of systems as requiring a platform approach. CIMdata has published a lot on platforms, usually in the context of a product innovation platform but platforms can also be developed for products such as automobiles and for services.[5] The original Harvard business review article written on platforms[6] identified connection, gravity, and flow as critical elements for a successful platform and also noted value creation for all platform participants. Digital inventory-as-a-service has both the requirements and solutions elements for a successful platform.
Wipro’s Solution and Role
Wipro has developed a digital inventory-as-a-service platform shown in Figure 1 which is currently focused on the oil & gas and marine industries. Wipro organized the platform to provide the underlying solution so appropriate stakeholders, consumers, and producers of spare parts, as well as the technology, regulatory, and material suppliers could exchange information and get product in a repeatable process. For example Wipro recruited DNVGL, an internationally accredited registrar and classification society headquartered in Norway that supports the target industries to support the alliance regulatory role. By focusing on an industry, Wipro was able get industrial customers to commit to the platform so there is enough demand for the platform to operate efficiently. The facilitation role played by Wipro to bootstrap the platform is a critical success factor that can’t be over stated.
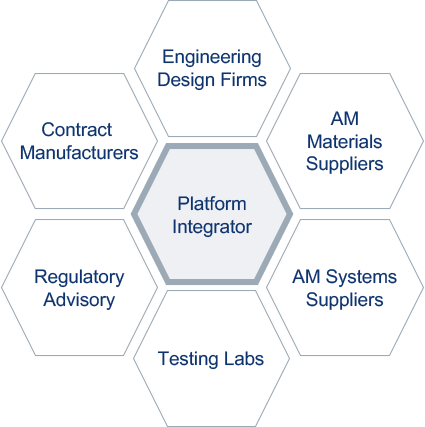
Figure 1 - Wipro Has the Role of Platform Integrator Within their Digital Inventory-as-a-Service Approach
(Courtesy of Wipro)
Wipro has assumed the role of platform integrator and matchmaker as they connect the platform participants. They have developed the relationships with all the stakeholders and developed solutions to enable digital inventory-as-a-service. The core of the service is the digital passport shown in Figure 2. The passport collects all the data necessary to produce a part quickly, reliably, and with proper certification.
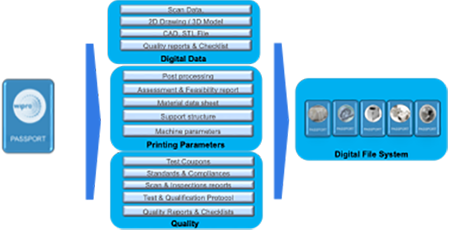
Figure 2 - Wipro's Digital Passport Captures and Manages all Relevant Data to Ensure Compliant Parts are Produced
(Courtesy of Wipro)
By connecting the industrial companies’ product data with certified contract manufacturers around the globe with the support of additive equipment providers and material suppliers everyone wins. Industrial companies can get critical parts made on demand and the additive manufacturing industry gets more business and improves technology.
While the platform is what most of enterprises are looking for, details matter. When companies connect to a spare parts platform, they have many enterprise solutions that need to be connected to operate efficiently such as SAP Ariba or other supply chain platforms. Wipro has the skills and solutions to manage not only the platform but solution integration from any of the platform participants.
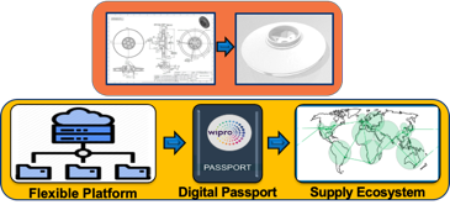
Figure 3—Wipro's Digital Inventory Differentiators
Courtesy of Wipro)
Figure 3 shows the critical elements of Wipro’s digital inventory solution. The platform that supports all participants, the digital passport which carries the details necessary to get certified parts produced and the supply ecosystem connecting equipment, materials, and contract manufacturers in a flexible network designed to optimized inventory management.
Conclusion
The spare parts inventory management process is ready for digital transformation. While many companies still have an opportunity to improve using existing spare parts management approaches, additive manufacturing is a new element that can drive significant improvement in the process. Leveraging AM requires many technologies to be organized, and the scale required for efficient operation is beyond that of any single company. Wipro’s industry focused digital inventory-as-a-service solution pulls together a consortium of stake holders to increase the business viability and adds technology to support validated part production by ensuring part identification, traceability and also ensuring that certified parts are reproduced reliably. CIMdata recommends that companies looking to transform spare parts management check out Wipro’s approach. The oil & gas and marine industry program is underway and other industries are in process.
[1] Research for this commentary was partially supported by Wipro.
[2] https://www.researchgate.net/publication/326718559_Spare_parts_inventory_control_-_an_overview_of_issues_for_a_large_industrial_complex
[3] https://www.conklindd.com/t-whatdoesinventoryreallycost.aspx
[4] https://www.hagerty.com/media/news/cadillac-blackwing-models-will-use-3d-printed-parts-like-this-shifter-medallion/
[5] https://www.cimdata.com/en/resources/about-plm/a-cimdata-dossier-plm-platformization
[6] Bonchek, Mark and Sangeet Paul Choudary. “Three Elements of a Successful Platform Strategy.” Harvard Business Review. Jan 31, 2013.