Key takeaways:
- While digital transformation and Industry 4.0 dominate the business headlines, improving global sustainability is also a major global imperative.
- Companies need to evolve their value chain strategy from focusing on logistics and costs to "responsible value chains."
- Accenture believes that to become responsible and transform the business value paradigm, businesses must become trusted, net zero, and circular, and smart, connected products will be essential to power that transformation.
- Smart, connected products will be an essential element to collect and interpret data necessary to help companies become trusted, net zero, and circular.
- Accenture Industry X solutions, services, and partner ecosystems are designed to help customers meet these goals.
This CIMdata commentary highlights the global need for drastic improvements in sustainability. Accenture, a leading global system integrator, has expansive goals for their own sustainability efforts and is transforming its Industry X practice to help their customers make equally impressive gains.[1]
Improving Sustainability is a Global Imperative
People the world over were riveted by the Apollo space program in the United States.[2] The Space Race kicked off in 1957 with Sputnik, the first satellite, and humans had raced around the world for years after that but Apollo took humans to the moon. The first picture of moonrise taken from Moon orbit showed a blue, pristine looking Earth that was already showing signs of environmental distress. The seeds of environmental activism were sewn shortly after this event. Earth Day was proposed at a UNESCO conference in 1969 and was first celebrated in the United States in 1970, and was taken international in 1990. Some observers draw a straight line from that beginning to the Paris Climate Accords in 2016.
Unfortunately, the good intentions from 50 years ago have not been realized, with not enough progress to show for the efforts applied. The world is swimming in the detritus of human existence. The Great Pacific Garbage Patch in the north Pacific Ocean spans from Japan to the United States. No one really knows how much waste is in the gyre[3]. Products from sea vessels to consumer electronics created in the West are “recycled” in countries like Thailand, that are choking on the volume and the environmental degradation that results.[4] A major environmental downside to the COVID-19 pandemic is the vast increases in packaging used for things like takeaway food and rapid growth in delivered items.
Product companies are being pushed to change on a number of fronts. Many efforts to make positive change are often led by the European Union and leading companies based there. For example, the Waste Electrical & Electronic Equipment (WEEE), the Restriction of Hazardous Substances (RoHS), and Energy-Related Products (ErP) standards levied new requirements for commerce in the European Union, a market too big for global companies to ignore. Concurrent engineering, an approach popularized in the 1990s that helps shorten product development by simultaneously considering a wide range of technical and organizational perspectives earlier in the development process, now includes consideration of reuse, recycling, and remanufacturing in what is termed “design for X” analyses.[5],[6]
Many of these ideas coalesced with the rise of the Circular Economy, an economic system focused on eliminating waste and the continued (re)use of resources. While the idea emerged in the 1970s, it is only in the last two decades that things took shape. For example, in 2006 China named circular a national policy in their 11th five-year-plan. This effort is championed by the Ellen MacArthur Foundation, founded in 2009 to focus on this issue, and has picked up steam in the last decade. Strategic partners of the Foundation include global heavyweights like Philips, Google, Ikea, Renault, SC Johnson, and Unilever. In 2014 at our global PLM Market and Industry Forum event CIMdata detailed how this initiative created significant opportunities for the Product Lifecycle Management (PLM) Economy, CIMdata’s term for the software and services companies that help industrial firms achieve their PLM objectives. CIMdata strongly believes that PLM initiatives and enabling technologies can provide significant new opportunities for industrial firms. In fact, CIMdata evolved the way we talk about the product lifecycle itself. Products should no longer have an “end of life” but should be managed from idea through life, with recycling and reuse an essential part of the product and manufacturing process definitions to help meet sustainability targets.
Sustainability initiatives often fall under corporate social responsibility (CSR) programs, which first emerged in the 1960s. Today environmental concerns top the list for many companies. Caterpillar, the world’s largest construction equipment manufacturer, has improvement goals for both their operations and their products. For example, in 2006 Caterpillar set a goal for 2020: reduce greenhouse gas emissions intensity by 50%. The company reached 54% in 2019.[7] On the product side, Caterpillar reported that 91% of eligible end-of-life returns were collected for remanufacturing. Global manufacturing giant Siemens is one of many companies that is focusing their sustainability efforts on global strategic needs, framed in part by the UN’s sustainable development goals (UNSDGs).[8] But the company sees improving sustainability as more than just corporate responsibility. “Committing to cutting our global carbon footprint is not only prudent—it’s profitable,” stated Mr. Joe Kaiser, CEO of Siemens AG.[9]
This is an important point. It is not enough for companies to want to reduce emissions, produce less waste, or remanufacture their products instead of scrapping them. The incentive to change is much stronger if you can see making positive change as a business opportunity. Accenture conducted an interesting analysis of the European automotive component and industrial equipment market, summarized in Figure 1. It highlights the potential value pools available by creating and leveraging more circular value chains. This analysis identified over $50 billion in annual possible expenditure reductions just in this industrial segment in Europe.
The urgent need to improve sustainability exists in a product world that is rapidly changing. Smart, connected products reign in many industrial markets. The companies that make them are making strategic investments toward achieving some version of the Industry 4.0 vision.
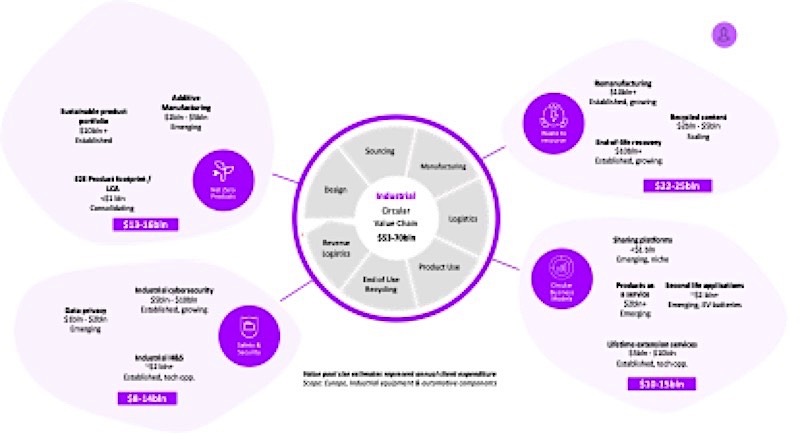
Figure 1—Opportunities in the European Industrial Equipment & Automotive Components Segments
(Courtesy of Accenture)
Companies need to manage dynamically changing global value chains to bring in needed innovation and often to better serve far-flung customers. Many see digital transformation as a critical enabler for thriving in this smart, connected future, often by creating new business models, such as product-as-a-service. CIMdata strongly believes that industrial companies pursuing such transformation really need a strong end-to-end product strategy and implementation to succeed. Fortunately, companies can leverage the same technologies and processes used in support of addressing these trends to help reach their sustainability objectives, particularly by transforming their value chains. These concepts include model-based systems engineering (MBSE), digital twin, digital thread, and the Internet of Things (IoT). Accenture’s Industry X practice stands ready to help.
Industry X and Responsible Value Chains
Accenture is one of the leading global system integration firms, with over 500,000 employees serving customers in more than 120 countries. CIMdata follows Accenture closely since they are the global revenue leader for services in our annual PLM market analysis, driven largely by their Industry X practice.[10] Accenture has grown organically and through acquisition to deliver products, Accenture-developed technology, and services to a wide range of industrial clients. Their PLM-related practice is in their Industry X unit, as is their Smart Connected Products group. According to Accenture, Industry X is their approach for helping clients “transform their business model and operations, re-invent their products from design and engineering, through manufacturing and support, to compete now and drive exponential growth.” Figure 2 highlights some examples of the types of strategic and tactical support that Accenture’s Industry X practices delivers to their customers.
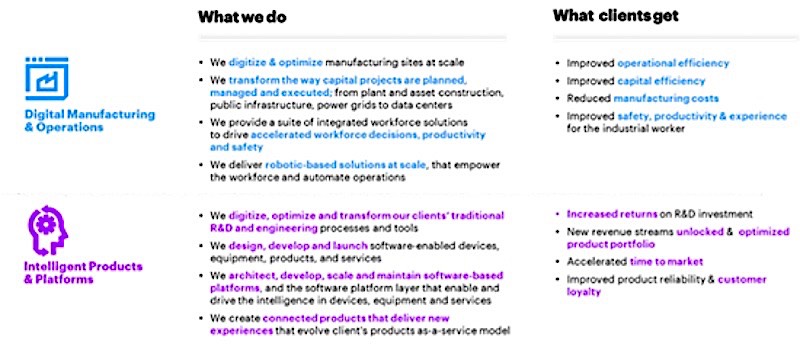
Figure 2—Examples of Accenture Industry X Efforts
(Courtesy of Accenture)
Accenture is another global giant that frames its sustainability efforts around the UNSDGs. Accenture collaborates with the UN on their CEO Study program, a joint review of sustainability efforts that seek to coalesce the views of global business leaders and UN executives. For their most recent study in 2019 Accenture interviewed over 1,000 top executives representing 21 industries and 99 countries about the opportunities and challenges to achieving the Global Goals.[11] Based on their research, 71% of CEOs believe that business must play a critical role in helping achieve the UNSDGs. Accenture and CIMdata agree that if industrial companies are to effectively contribute to meeting these ambitious goals smart connected products, the IoT, and PLM-related solutions will play leading roles.
A key concept to Accenture’s approach is what they term responsible value chains which is part of the firm’s new holistic “360°” value framework.[12] According to Accenture, responsible companies share three primary characteristics, as illustrated in Figure 3. First, they must be “trusted,” with a focus on creating products, and their associated supply chains, in ways that drive equitable growth and increase the quality of life for their employees, customers, and communities. Effectively addressing health, safety, and ethics issues is essential in such organizations. This will be a new consideration for many companies defining their value chains. Second, firms must strive to be “net zero,” with greenhouse gas-neutrality of both products and their production and operations. This will also require significant change. While CSR programs are common at the large companies at the top of many value chains, adoption will have to expand in their tiers of suppliers. Finally, responsible companies must be circular. This will require significant rethinking of the entire product lifecycle from idea through life. Companies will be more likely to pursue circular if its objectives are also of interest to its customers. There is some evidence that consumers are increasingly considering environmental concerns in their purchasing decisions.[13] To help their industrial customers meet these significant challenges, Accenture designed a set of solutions, services, and partner ecosystems focused on sustainability and creating responsible value chains that are delivered by their global Industry X practice. Their efforts are already bearing fruit for their global clients.
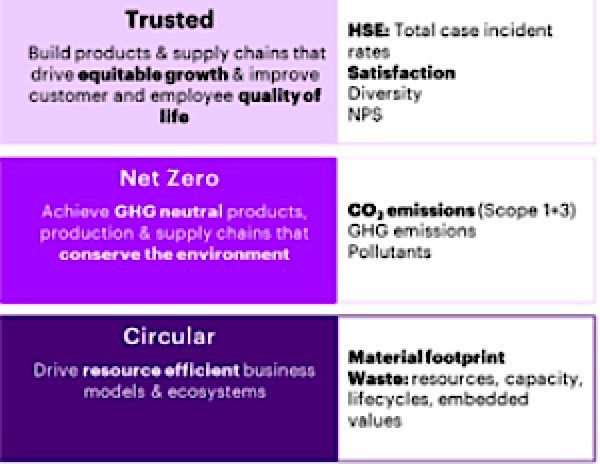
Figure 3—Key Characteristics of Responsible Companies
(Courtesy of Accenture)
Some Accenture customer examples will help make their client interactions more concrete. Accenture’s work with a global automotive supplier offers a good example. The company set an audacious goal: to develop a corporate CO2 platform to track the CO2 impact of their environmental initiatives. This “single source of truth” would help them measure their CO2 footprint and to support decision-making across their value chain. The client’s goal was to be carbon neutral by 2030. Accenture modeled key scenarios that spanned engineering, procurement, and design to inform and involve key stakeholders. They expanded their communication strategy to include Webinars to educate employees that translated carbon neutrality concepts to fit the company context. Accenture also helped to build consensus on key enablers for carbon neutrality and built a roadmap complete with cost estimates. When complete, the platform will draw on multiple trusted data sources to calculate the client’s footprint, support developing and executing their carbon reduction roadmap, and track and monitor the results using internal dashboards and custom reporting for external stakeholders.
The Biesse Group (Biesse), an Italian specialist in industrial equipment in the woodworking segment, saw the opportunities that the IoT/IIoT offered for both them and their customers. The company has a history of investing in software and advanced services, and is known for developing easy-to-use solutions that make using their advanced manufacturing technology more practical for their customers. Connected asset management leveraging the IoT could help improve operational efficiencies, reduce costs, and open up new revenue streams. Accenture worked with Biesse to design an IIoT operating model, business case, and solution roadmap. The overall goal was to improve machine productivity and customer satisfaction by minimizing downtime through predictive maintenance powered by in-depth analytics. This helped Biesse by optimizing both processes and economic activities in real time, reducing the consumption of all types of resources.
The platform enables sending real-time information and data on the technologies in use, optimizing the performance and productivity of machines and systems. The data collected support detailed analyses of production process and machine functions, detecting malfunctions, assisting customers in maintenance operations, ordering replacement parts in less time and ultimately preventing faults.
Initial services focused on preventive maintenance alerts, machine management, manufacturing events analysis, and remote software distribution. Energy management was significantly improved since the solution monitor the consumption and was able to rectify usage in real time. Many services are planned to be introduced in the future.
Accenture drastically shortened the time to value for Biesse by building their customer-facing IIoT solution using the Accenture Connected Platforms as a Service (CPaaS) on the Microsoft Azure IoT platform. Using this approach, the company was able to deploy the solution in only five months. Sensors and devices on the machines produce in-depth analytics for display on easy-to-view dashboards using Microsoft Power BI data visualization on mobile devices. Significantly more functionality is planned. Once fully rolled out, a pay-per-use model will allow Biesse’s customers to customize the services they receive.
Conclusion
Climate change and environmental degradation have made improving sustainability top of mind for many companies and governments. Accenture, a leading global system integration firm, is one of many global companies setting lofty sustainability goals for their own operations and products. Reaching these sustainability goals can be challenging but another overarching trend, the move to smart connected products in many industries, actually provides technology and processes that companies can leverage to help reach those lofty goals. CIMdata sees product strategies and enabling technologies as core to the solution needed for industrial companies. To Accenture, a leading global systems integrator, these issues and enabling technologies are core to the mission of their Industry X practice, which can draw on intellectual and human assets from across Accenture to help companies achieve their sustainability goals. The global automotive supplier and the Biesse Group are just two of many Accenture customer examples. Accenture’s objective of enabling responsible value chains is exemplary of what needs to happen more broadly in society and commerce. Only through collective action can we all strive to remake the Earth into that beautiful blue ball first viewed in the moonrise over fifty years ago.
[1] Research for this commentary was partially supported by Accenture.
[2] “The Apollo 11 Mission Was Also a Global Media Sensation,” https://www.nytimes.com/2019/07/15/business/media/apollo-11-television-media.html
[3] https://www.nationalgeographic.org/encyclopedia/great-pacific-garbage-patch/
[4] https://www.pri.org/stories/2019-05-21/your-recycled-laptop-may-be-incinerated-illegal-asian-scrapyard
[5] E.g., Fleischer and Liker (1997). Concurrent Engineering Effectiveness: integrating product development across organizations. Hanser Gardner Publications. Cincinnati, OH.
[6] E.g., design for assembly, design for manufacturing, design for disassembly, etc.
[7] https://reports.caterpillar.com/sr/2019_Caterpillar_Sustainability_Report.pdf?_ga=2.262491460.994540390.1602188691-2025495101.1602016119
[8] https://sdgs.un.org/goals
[9] https://new.siemens.com/th/en/company/sustainability/decarbonization/carbonneutral.html
[10] Accenture chose the name “Industry X” because ”technology now is in such dynamic flux that its staging posts can no longer be pinned down for longer than a moment.” Eric Schaeffer. Industry X.0: Realizing Digital Value in Industrial Sectors. Germany. Redline Verlag. 2017.
[11] The Decade to Deliver a Call to Action: The United Nations Global Compact—Accenture Strategy CEO Study on Sustainability 2019. https://www.accenture.com/_acnmedia/pdf-109/accenture-ungc-ceo-study.pdf
[12] Change Powers Accenture’s Biggest Brand Move in a Decade. https://newsroom.accenture.com/news/change-powers-accentures-biggest-brand-move-in-a-decade.htm
[13] Sustainability in packaging: Inside the minds of US consumers.” McKinsey & Company. October 2020.