Key takeaways:
- PLM is finally gaining momentum in its move to the cloud as security and performance concerns are addressed. The COVID-19 pandemic and work-from-home are accelerating the transition.
- Enabling CAD and PLM on the cloud, requires a complex mix of hardware, software, processes, and data to work in harmony—not an easy task.
- HCL's 1PLMCloud supports a matrix of software solutions that have been designed to enable manufacturing companies’ digital thread requirements and remote work challenges. The modular end-to-end service offering includes initial consulting, deployment, and operations support.
- 1PLMCloud enables remote work and scalable, secure, and agile operations while reducing total cost of ownership of engineering IT infrastructure and services.
Product Lifecycle Management (PLM) is finally ramping up on the cloud. Many of CIMdata’s customers have roadmaps for cloud deployment but they are commonly multi-year endeavors. Even a medium-sized company can have several hundred applications running in the data center forcing real planning to happen before a meaningful cloud transition can take place. CIMdata’s research over the last few years has shown interest, opportunity, and some early adopter movement but it appears the COVID-19 pandemic will be the catalyst to take it mainstream.1
While cost saving has been a big driver for the move to cloud, the remote working reality many of us have experienced since March 2020 has demonstrated the need for improved access to and performance of enterprise, as well as desktop PLM-enabling solutions. When remote working started, many IT professionals held their breath to see what would fail. Would home network connections be able to handle the corporate information load? Would corporate internet connections and infrastructure be able to handle the load? Fortunately, the technology worked, and most companies were able to manage issues reasonably well.
While most enterprise applications are able to operate on the cloud using platform-as-a-service (PaaS), CAD and PLM solutions have lagged behind. The current cloud native PLM solutions work best for products that don’t have complex CAD data. The file-based architecture of most CAD applications requires that data be accessible via LAN speeds of 100Mb to multi-Gb transfer rates with low latency. Individual product models can be tens of megabytes and complex products can be represented by thousands of files requiring tens or even hundreds of gigabytes. While this may not seem daunting when cloud providers are talking about managing hundreds of exabytes, they generally are not copying much data from one storage area to another.
To support local CAD file requirements, product data management (PDM) solutions often copy data from a vault into a local folder on the user’s desktop device. This copy is where edits happen, and the resulting data is synchronized with the server when the file is “checked in.” Moving files back and forth to a data center server over complex public internet routes can be slow and cause issues with older client-server protocols. A hiccup in the data transfer or timeout driven by latency can cause uploads to fail, and when a single file in a group fails, the whole transfer often fails and must be restarted. The older the PDM solution, the more prevalent this issue is.
Licensing can also be an issue. User licenses are usually computer specific or server based. Getting license access through firewalls and VPNs can be complex, and sometimes just doesn’t work. Fortunately, software companies are flexible and as part of COVID-19 support programs, most are supporting companies with temporary licenses.
Perhaps the most interesting issue CIMdata has run across is with companies that have strict security requirements such as International Traffic in Arms Regulations (ITAR) and Export Administration Regulation (EAR). PLM implementations that support these requirements don’t allow remote access, reducing the risk of a breach. One client commented “we never planned on having to operate in a work-from-home (WHF) environment.”
Multi-discipline CAD such as NX, CATIA, or Creo solve difficult product development challenges but are themselves often complex to configure and operate. The data they create and what is managed with PLM can also be rather complex.
For CAD and simulation users, desktop workstations are the norm. These computers are usually configured with the fastest CPUs, high-end graphics cards, double and even triple monitors, and a significant amount of RAM. When practical, some users brought these systems home to keep working during the pandemic, but in many cases, they are being accessed using a remote display protocol. Essentially, the workstation resources run the application on the office computer and the pixels are sent to the remote screen at home. Remote Display Protocol (RDP), a protocol native to Microsoft Windows performs reasonably well, and has worked admirably in the current remote work environment. NVIDIA, a leading graphic card supplier, released an update that enables 3D graphics to be shared via RDP, dramatically improving performance for those accessing workstations with NVIDIA hardware.
Virtual Desktop Interface (VDI) is a more advanced proprietary solution implemented at some companies. It virtualizes both CPUs and GPUs. Computer room racks contain servers with compute and graphic hardware with VDI software that partitions the resources into virtual workstations. The flexibility of being able to share CPUs and GPUs is cost effective for low performance needs and the ability to aggregate multiple CPUs and GPUs together enables high performance needs to be met with the same solution. The VDI infrastructure is usually co-located with the PLM solution so data access is done at data center speeds, and only pixels are at the mercy of the internet. For companies that have this infrastructure in place, WFH is relatively easy to support as long as internet bandwidth is available.
The most recent iteration of remote desktop technology is the cloud workstation. Essentially, it is VDI implemented by a cloud provider such as Amazon Web Services (AWS) or Microsoft Azure which complements PLM solutions in the cloud whether cloud native or when leveraging infrastructure-as-a-services (IaaS) solutions. The big benefit is that companies no longer need to implement and support any PLM infrastructure, cloud workstations access PLM data at data center speeds and fully leverage the cloud. While there still may be last mile issues, users are able to leverage the internet backbone as most major internet service providers (ISPs) have high-quality connections to major cloud providers.
The cloud workstation accessing cloud-based PLM solutions is an elegant solution. It provides predictable high-speed access to data and applications for any remote user with a reasonable internet connection. Performance is addressed by fast data access and workstation configuration flexibility. Equally important, security is addressed since data never leaves the data center, only computer display-specific information is transmitted. This approach also reduces complexity by eliminating distributed data and simplifies workstation configuration.
HCL recently briefed CIMdata on their new 1PLMCloud offering. Cloudification has been underway for a decade, and CIMdata has chronicled the interest, advancing technology, and growing adoption. 1PLMCloud from HCL is the latest advancement in PLM cloudification delivering a fully integrated PLM-as-a-Service solution. There are three products within the offering:
- xCloud—System Integration services including consulting, transformation, and operations
- DesignCloud—Managed services leveraging public cloud based on annual subscription per user, customization, and integration
- EngineeringCloud—Pay-per-use model based on number of users and per hour pricing
HCL’s 1PLMCloud offering spans the continuum of customer needs and supports leading CAD and PLM solution platforms from Siemens, PTC, and Dassault Systèmes hosted on leading cloud platforms from Amazon, Microsoft, and Google. xCloud has been designed for companies with their own cloud accounts and providers. DesignCloud has a managed services and annual subscription approach where HCL owns cloud accounts and resells CAD and PLM licenses. The innovative EngineeringCloud solution has a pay-per-use SaaS model where HCL makes licenses available in smaller increments. CIMdata is impressed by the packaging of the technology with the SaaS approach as it is a significant simplification of the PLM environment from the customer perspective.
HCL has Enterprise, Standard, and Basic offerings designed for OEMs and Tier-1 suppliers based on number of users, data capacity, geographical spread, and an SLA for resolution priority, which are typical for cloud offerings. As HCL approach is designed to support complex PLM implementations typical of OEMs and Tier-1s, it needs to support complex and customized solution implementations. HCL has several tools to help support and administer this type of environment such as Active Tester DevOps solution, BOT solutions (software to automate common admin tasks), PLM migration cockpit, PLM upgrade toolkit, data migration toolkit, and data validation toolkit.
CIMdata is pleased to see HCL’s PLM DevOps and Active Tester, as illustrated in Figures 1 and 2, included within the offering. We believe this is a critical strategy for companies to implement so they can maximize the ROI of their PLM solutions. By using DevOps and Test Automation in conjunction with agile development, capabilities requiring adjustment aligned to business changes and opportunities can be more easily realized.
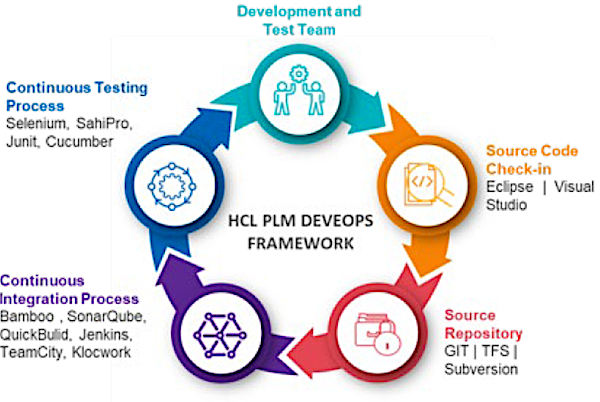
Figure 1––HCL's DevOps Approach (Courtesy of HCL)
Figure 2––HCL's Test Automation Approach (Courtesy of HCL)
The upcoming EngineeringCloud solution is significant as HCL owns all infrastructure, including the software licenses. When combined with the infrastructure, including cloud workstations, all available via the cloud in a pay-per-use model, a big shift in business operations can happen. Such an approach allows companies to add and drop users based on project needs, and subcontractors will get cost effective access to tools and can be easily integrated into projects with little dependency on location. CIMdata is really looking forward to seeing this vision become a reality, and we should see early results soon as HCL ramps it up.
Planning, configuring, deploying, and operating an enterprise PLM solution for hundreds or thousands of users is not a trivial effort. Diverse and deep specialist skills are required to be successful. HCL has used their system integrator skills and PLM competency to develop a solution to manage one of the very complex issues with migrating PLM to the cloud–moving CAD data to the cloud.
Companies looking for help getting a mindshare leading PLM solution running on the cloud should check out HCL. Their 1PLMCloud solution combines complex PLM solutions and CAD technology with leading system integration services to help customers take their enterprises forward on the cloud.
1 Research for this commentary was partially supported by HCL.