Key takeaways:
- 3D Sweep leads a list of productivity and usability enhancements in Creo Parametric 5.0.
- Improvements in both additive and subtractive manufacturing include a partnership with Materialise to support metal 3D printing.
- A smooth workflow process for topology optimized models that automatically fits precise geometry to the approximate planar mesh.
On March 19, 2018, PTC announced the release of Creo Parametric 5.0, the latest version of their flagship computer-aided design (CAD) solution. In its introduction, PTC executives highlighted three strategic areas of enhancement in the software—Productivity & Usability, Additive & Subtractive Manufacturing, and Simulation & Optimization. The collective improvements promise to enable “companies to accelerate product innovation and build better products faster by reusing the best designs and replacing assumptions with facts.” CIMdata agreed, lending the following quote to the official PTC press release: “PTC is on the leading edge of some of the hottest technologies today with the Internet of Things (IoT) and augmented reality (AR), but it has not forgotten its roots in CAD, instead transforming this business by infusing its leading Creo software with new technologies and capabilities,” stated John MacKrell, Chairman, CIMdata.
Productivity and Usability
This class of enhancements is headlined by the introduction of 3D Sweep. The operation of 3D sweep allows the designer to take a solid model component or a simple geometric solid and propagate it along a 3D trajectory. See Figure 1. Using this capability, the designer can carve out a 3D spatial volume that can be used for numerous purposes from defining a path for a component in a moving mechanism to creating an accurate 3D model of a part machined with cutting tools. CIMdata believes that 3D Sweep is one of the more formidable tools in a CAD solution’s modeling arsenal and commends PTC for its inclusion in Creo.
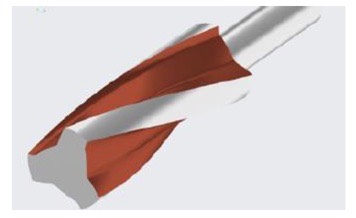
Figure 1—A 3D Sweep along a Helical Path (Courtesy of PTC)
In addition to 3D Sweep, Creo supports an enhancement for the application of draft to model surfaces that already have rounds applied. The proper solution is to first remove the rounds, perform the draft, then reapply the rounds but when done manually the designer can often forget how the rounds were placed. This is especially true for imported models that a designer did not create in the first place. The new Creo capability automates the procedure by removing and reattaching the rounds.
Another noted enhancement that designers will appreciate is Creo now allows design actions to be performed within a perspective view, as shown in Figure 2. The user can display the current model in a perspective view and interact with it as they work on the model.
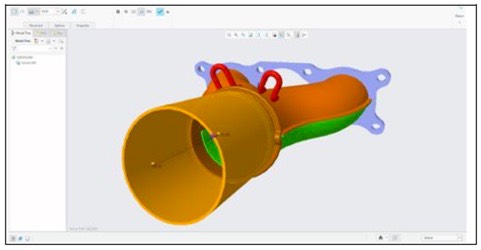
Figure 2—Design in Perspective View (Courtesy of PTC)
Additive and Subtractive Manufacturing
In additive manufacturing with Creo 5.0, PTC reports they now support approximately 70 percent of available 3D printers. This includes the introduction of the Creo Additive Manufacturing Plus Extension for Materialise, which extends 3D printing capabilities to metal parts. The ability to support the generation of 3D printed metal parts allows users to print production-grade parts directly from Creo. A further benefit of the extension is that it allows users to connect to the Materialise online library of print drivers and profiles expanding PTC’s coverage. CIMdata strongly supports this partnership with Materialise which has elevated it to be a serious player in the 3D printing market.
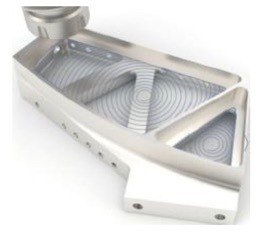
Figure 3—Mold Machining (Courtesy of PTC)
In subtractive manufacturing, the new Creo Mold Machining (Figure 3) extension supports dedicated high-speed, multi-threaded machining capabilities optimized for molds, dies, electrodes, and prototype machining.
Simulation and Optimization
Creo 5.0 now offers users three levels of Computational Fluid Dynamics (CFD) solutions targeting engineers up through expert analysts as illustrated in Figure 4. The Creo Flow Analysis Extension base solution supports analysis types of flow, heat, and turbulence with calculations for internal and external flows. The solution offers animation of flow results in real-time and parallel processing simulation. The next level of solution, Creo Flow Analysis Plus, adds analysis types of particle, radiation, species, and moving/sliding meshing. The top-level solution, Premium, targets analysts and supports cavitation, multiphase, multicomponent, and dynamics.
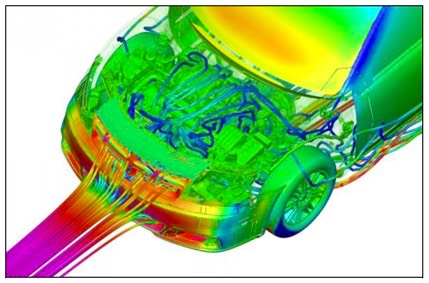
Figure 4—Creo 5.0 CFD (Courtesy of PTC)
For Topology Optimization, PTC has teamed with Vanderplaats Research and Development, Inc., (VR&D) to offer a solution based on VR&D’s Genesis product creation engine. The user specifies keep areas, loads, constraints, and sets optimization goals then runs the topology optimization algorithm to compute a product model solution. The optimization is fully integrated within Creo and supports structural, modal, and thermal analysis.
PTC’s strongest contribution is the ability to automatically fit precise surfaces to the optimization’s output tessellated mesh geometry. CIMdata believes this approach may offer PTC a leadership position in topology optimization but will require close attention to the quality of the automatic fitting algorithm so as to provide usable precise geometry.
Summary
Creo 5.0 will be a welcome release for Creo users who may have felt forgotten given PTC’s recent focus on Internet of Things (IoT) and Augmented Reality (AR). CIMdata believes the release is a refreshing advance for PTC highlighting their technical expertise across all the important areas of productivity, manufacturing, and simulation.